XSPEE3D: The Next Generation of Expeditionary Metal 3D Printing
- SPEE3D
- Nov 8, 2022
- 4 min read
SPEE3D has released their next generation of expeditionary cold spray technology, called XSPEE3D. Unlike other 3D printers, XSPEE3D has all the printing capability and auxiliary equipment within one standard shipping container, making it the world’s most deployable metal 3D printer. With XSPEE3D, defense forces and other industries working remotely such as Oil and Gas, Mining, Maritime, and Agriculture, can maximize productivity, strengthen inventory, and generate parts when and where they are needed quickly in any location.
The product was developed based on the company’s extensive field work and collaboration with the Australian Army. Providing a revolutionary new way on how the military, and other industries, can source their own spare parts out in the field.

Integrated with SPEE3D’s patented supersonic cold spray deposition technology, XSPEE3D is 1,000 times faster than other additive manufacturing options, able to fabricate parts in just minutes. It can print one or multiple parts at once, up to 90 lbs and 40” x 30” in diameter, at rapid build rates up to 3.5oz a minute. XSPEE3D is safe and easy to use, install, and deploy, requiring only a connection to electrical power, and can fabricate parts immediately when live.
XSPEE3D overcomes a number of barriers when 3D metal printing out in the field, as its containerized, ruggedized hardware and unique cold spray process offers a reliable solution for rapid prototyping and production in remote locations or harsh conditions. Unlike other metal printers, XSPEE3D can cold spray quality 3D metal parts from over 12 metal alloys, including copper, stainless steel, titanium, high-strength aluminum, and nickel-based carbides, and can withstand extreme heat and rough terrain in the field.

XSPEE3D In Action: Defense Use Cases
For years, SPEE3D’s technology has been tested, validated, and used by Australian, US, and British defense forces to overcome various barriers when 3D printing; and when it comes to sourcing spare parts in the field, or out at sea. One of the most significant issues the military faces today is the ability to resolve critical spare part requirements in the field, a challenge that worsens with disruptions in the global supply chain.
Seeing the need to strengthen existing internal supply chains, SPEE3D’s cold spray technology has been used for a wide variety of defense use cases. It was first adopted by the Royal Australian Navy to manufacture and certify metal 3D printed marine applications for an Armidale-class Patrol Boat, and next by the Australian Army, which included trialing the technology’s expeditionary capabilities out in the field. This led to the Australian Army conducting metal 3D printing trials of their WarpSPEE3D tactical printer at Mount Bundey and Bradshaw. Through these trials, the Australian Army were able to successfully demonstrate how metal 3D printing can be deployed to the front line, and how SPEE3D technology can offer defense the self-supporting operational capability to manufacture their own metal 3D printed parts in minutes, on demand.
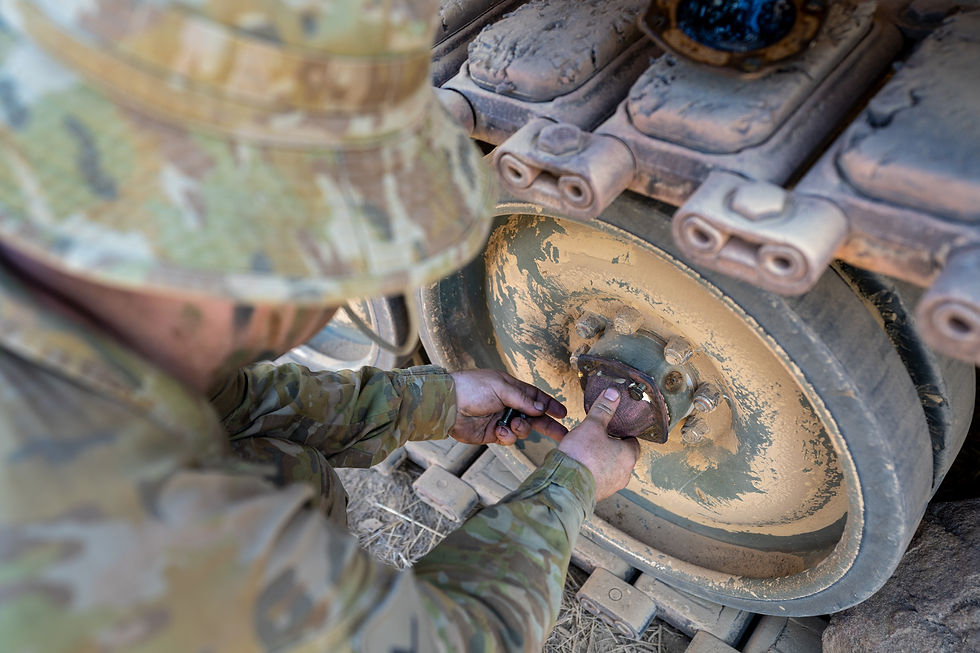
Following the success of these trials, SPEE3D technology has also since been utilized by the US Navy and British Army. SPEE3D’s WarpSPEE3D printer became the first in the world to successfully print dozens of parts for a US naval ship as part of the NCMS (National Center for Manufacturing Sciences) REPTX exercise, enabling the new possibility for military ships to become their own self-sufficient manufacturing hubs. Then most recently, SPEE3D’s WarpSPEE3D metal 3D printer was used by British Army REME soldiers for a multi-national training force as part of a concept assessment in tandem with the US Army’s Project Convergence Program.
Like SPEE3D’s other printers, XSPEE3D is embedded with SPEE3D’s patented cold spray process, a technology that uses supersonic deposition in which a rocket nozzle accelerates air up to three to four times the speed of sound. Injected metal powders are deposited onto a substrate that is attached to a six-axis robotic arm. In this process, the sheer kinetic energy of the particles causes the powders to bind together to form a high-density part of a near net shape in just minutes. Because of this process, along with being rugged, and easier to deploy, XSPEE3D can reliably manufacture large parts for various expeditionary applications and situations that would otherwise be unsuitable using other metal additive manufacturing methods.

Defense is often faced with various operational, economic, and supply chain issues. XSPEE3D provides the military an alternative tool for efficient logistics and supply management when sourcing spare applications. XSPEE3D can help the military produce metal parts when they are needed, and reduce the need for personnel to carry large stocks of spare parts for military vehicles, infrastructure, and other systems.
XSPEE3D is a versatile, rugged, and non-complex containerized metal 3D printer that can significantly leverage the way the military can now manufacture internally, and generate replacement parts for critical scenarios. XSPEE3D is the latest development in expeditionary metal 3D printing and helps overcome various issues that the military faces, including supply chain problems and disadvantages with traditional manufacturing methods. If you are interested in learning more about how SPEE3D technology can help your organization, please contact SPEE3D Contact.
Comments