What Are Antifouling Hull Coatings?
- VRC Metal Systems
- Sep 7, 2022
- 4 min read
Updated: Nov 8, 2023
Fouling is the deposition and accumulation of unwanted material on surfaces exposed to fluids. These unwanted deposits can include scale, insoluble salts, proteins, bacteria, algae, zebra mussels, and other aquatic organisms. Fouling is an issue, not only for marine vessels but also for heat exchangers, cooling towers, piping, or any industrial equipment subject to stagnant water or flowing fluids.
Factors that affect the accumulation of these materials include exposure to untreated water, the water pH, microorganism levels, aquatic organism levels, product viscosity, the roughness of component surfaces, and others. The direct effects of these accumulations can include decreased flow, decreased thermal exchange, increased drag along the affected surfaces, and corrosion. The indirect costs associated with fouling include slower throughputs and increased fuel and energy consumption.
Several types of antifouling hull coatings apply directly to marine vessels. There are also coating applications designed for industrial equipment. To learn how to employ these advances in cold spray technology, contact VRC Metal Systems.
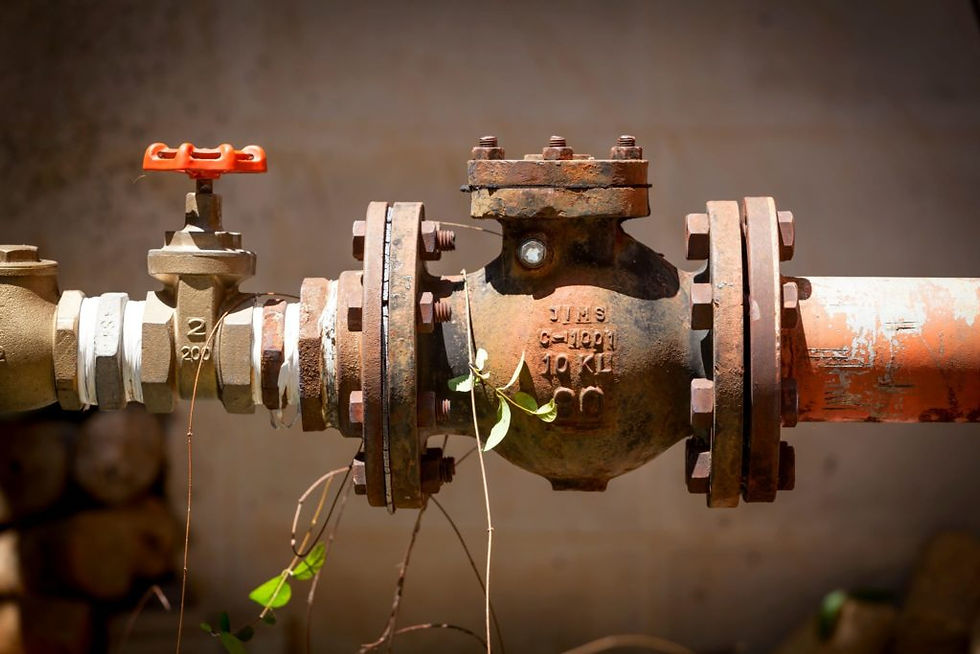
Types of Fouling
There are four general types of fouling:
Chemical fouling happens when a chemical reaction results in an unwanted layer of material adhering to the surface. A typical example of chemical fouling is when salts or dissolved solids such as calcium carbonate are deposited due to temperature and pH levels. Limescale is one such example.
Deposition fouling is also known as sedimentation fouling and occurs when particles fall out of the fluid and deposit themselves onto a surface. This outcome is usually a result of a slowed fluid flow.
Corrosion fouling happens when corrosion products form an added layer to the original surface.
Biological fouling is the settling and growth of aquatic organisms on any submerged surface, such as a ship’s hull. This type of fouling is most commonly associated with marine vessels, and hull coatings are the most common prevention method. Vessels with such fouling experience significant added drag, which increases fuel consumption. This, in turn, causes higher emissions of carbon dioxide, nitrous oxides, and sulphur compounds from the sulphur present in many marine fuels.
Note that corrosion itself can occur under any fouling conditions listed above. You can use cold spray applications to repair these surfaces or add a corrosive-resistant coating to inhibit future damage.

The Impact of Fouling
The impact of fouling is not to be taken lightly. Decreased efficiency and increased drag result in growth in fuel consumption by as much as 40%. According to the Office of Naval Research, in addition to increased drag, barnacles can add up to 150kgs per square meter in six months, further driving up fuel needs.
Then there are the cleaning, treating, and maintenance costs to consider. Biofouling of ships has cost the Navy upwards of $56 million per year on one class of mid-sized surface vessels alone for cleaning, hull paint, and fueling.
Types of Antifouling Hull Coatings Hull coatings aim to control surface roughness and minimize drag. Preventing the attachment and growth of organisms contributes to this better surface roughness and eliminates any increase in weight.
Wooden ships were protected with copper sheaths below the waterline. Copper kills many organisms in prolonged contact, keeping the vessel free of fouling and protecting them from “shipworm” attacks. However, when modern ships of steel were built, the copper would cause galvanic corrosion and could not be used. New antifouling paints were developed in response. Some coatings slowly dissolve over time so that any adhered organisms fall off. These coatings require replenishment relatively often, which can be problematic on large ships.
Another common anti-biofouling approach on marine vessels uses a biocidal coating that kills organisms that try to attach to the hull. A soluble coat system will dissolve in the water to release the antifouling toxins. Insoluble bottom paint doesn’t dissolve but still discharges the toxins.
In either case, the biocides dissolve and migrate into a layer close to the ship’s hull, creating a toxic barrier at the surface. However, many of these coatings have been shown to cause widespread pollution of biocidal material, causing harm to a range of marine life, and replacements are sought.
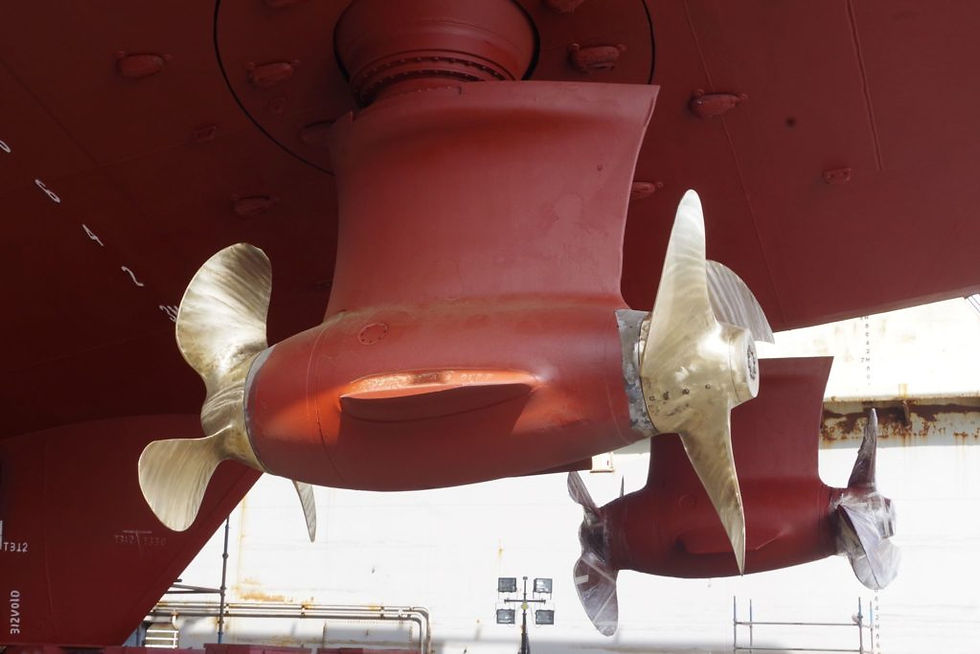
The Future of Antifouling
Copper is getting another look because of its high performance. To avoid galvanic corrosion, an electrically insulating film is needed between the copper and the steel hull. This insulation can be accomplished using cold spray.
First, you need to deposit a layer of polymer material onto the steel hull. Then a blend of polymer and copper particles can be deposited on top. Using the blend of polymer and copper also lets you deposit onto nonmetallic hulls, especially fiberglass hulls.
Applying corrosion-resistant coatings can also repair and prevent different fouling mechanisms in other areas, such as water intakes for industrial processes, diesel fuel storage tanks, heat exchangers, and many others.
You can also apply cold spray corrosion-resistant coatings to repair corroded surfaces and prevent future corrosion, thereby preventing corrosion fouling in both marine and industrial settings.
Contact VRC Metal Systems, a proven leader in this emerging industry, to learn more about the antifouling applications of VRC Cold Spray in your industry.
Comments