Tantalum and Niobium Powders for Cold Spray Applications
- Global Advanced Metals
- Jul 18, 2022
- 9 min read
Updated: Jul 20, 2022
Dr. Matthew Osborne, R&D Manager of Metallurgical Technology
Abraham Calvin, Sr. R&D Engineer
Cold Spray Technology
Cold spray is a variation of thermal spray technology where fine metal powders are carried by a
supersonic gas stream to strike a substrate and form a conformal coating. Unlike thermal spray,
cold spray particles impact the substrate as solids rather than liquids, and bond due to solid flow
and interlocking of the particles with each other, and with the substrate. Layers can be built to
almost any thickness and the varieties of materials and applications are numerous. The unique
bonding interface and lower temperature interaction is opening the door to new material
systems and opportunities. In many applications, heating from weld repair or traditional thermal
spray can be detrimental to the substrate, giving cold spray an advantage as an in situ build or
repair method. Many excellent references such as Practical Cold Spray[1] can provide overviews
and detailed studies of cold spray. Figure 1 shows a general schematic of the cold spray
equipment and process.

Fig. 1 General cold spray schematic [2].
Cold spray of metals onto surfaces is finding many advantages. As mentioned above, cold spray
enables the ability to perform repairs with minimal thermal impact, eliminating the need for postrepair heat treatment. Eliminating thermal treatments permits point-of-use repair, making cold spray extremely attractive in applications such as keeping military vehicles in service[3, 4]. As many legacy military programs face the challenge of component obsolescence, it is becoming
imperative to sustain critical component inventories; however, cold spray has the potential to
reduce the need to replace components with new, impacting obsolescence[5]. Cold spray is
demonstrating the unique ability to combine materials with different properties (e.g., yield
strength, melting point, corrosion resistance) to form graded layers[6] or a blended mixture such
as a hard-phase / soft-phase composite for the replacement of electroplated hard coatings[7]. Cold spray processing and materials have been developed for aerospace[8], a large number of military applications[9, 10], and to address extreme environments in energy generation[11, 12, 13]. As cold spray becomes a standard repair and build technology, the number and variety of applications and materials will increase.
Applications for Tantalum and Niobium
Tantalum (Ta) and Niobium (Nb) are well known for their corrosion resistance and refractory
properties. They are commonly used unalloyed in electronics, semiconductor manufacturing,
medical, and specialty chemical processing applications where superior properties are required.
Tantalum has a long history in medical applications[14] and its use continues growing due to its low toxicity[15, 16], osteointegration capability[17], and radiopacity[18]. In military applications, tantalum is used in durable electronics capacitors, munitions19, and has also been tested to extend the life of gun barrels[20]. Tantalum fills important roles in defense and is considered a critical strategic material[21].
A review of literature shows continued testing of cold sprayed Ta and Nb in critical military[22] and energy applications[23]. Due to the nature of these metals, they are easy to forge and roll at low temperature using traditional metal forming methods. This workability has translated to ideal
cold spray deposition performance, achieving near fully dense materials with strong, cohesive
layers with superior mechanical and corrosion resistant properties[22, 24, 25]. Forming surface
coatings via the cold spray process captures the benefit from tantalum’s and niobium’s corrosion
and thermal resistant properties while maintaining the strength, lower weight, and lesser costs
of the underlying substrates. For example, an iron-based or nickel-based plate or pipe can be
coated with Ta to allow more economical use in acid processing. Many applications for Ta and
Nb are known and the general expansion of cold spray will assist in growing the use of these
metals and their alloys.
Powder Requirements for Cold Spray
Cold spray is a straightforward process; particles impact a surface at velocities high enough to
deform and flatten the particles, expose nascent surfaces for bonding, and fill the surface
topography to prevent porosity. A number of operational and material parameters influence this
process, and need to be carefully controlled to repeatedly create strong, dense, and continuous
coatings with high deposition efficiency (DE = the amount of sprayed powder that is incorporated to the deposit; ~yield). The key powder characteristics for unalloyed metals include: 1. powder flowability, 2. particle diameter and shape, 3. particle microstructure and porosity, 4. gas impurities, and 5. the powder surface.
1. Powder flow is important for controlled feed into and through the cold spray system,
though the standard flow measurement methods are not perfect indicators of usability[26].
For a given material, powder flowability is a function of particle size distribution (PSD),
shape, and surface. Narrower size distributions flow more readily[27]; equiaxed shapes like
spheres and cubes flow easier than irregular particles[28, 29]; and rough, dirty, or damp
surfaces increase interparticle friction and inhibit motion[26, 30]. Superior cold spray
powders will have consistent PSD and particle shapes, low and controlled gas contents,
and clean, dry surfaces.
2. Particle size and shape also influence particle acceleration in the cold spray gas stream
and the impact energy at the substrate. For a given particle diameter (diameter is used,
even for nonspherical particles) there is a critical velocity[31] resulting in impact which
deforms the particle sufficiently to create fresh metal surface and fill voids, while not
being excessive and causing substrate damage. It is obvious that a very wide size
distribution will result in particles moving both faster and slower than the optimal spray
parameters resulting in less desirable deposit density and surface conditions. Particle
shape provides a similar effect with more and less aerodynamic particles having different
critical velocities (and deposition efficiencies) and causing similar variations in deposit
quality. Maintaining consistent size and shape of the particles is critical for maintaining
optimized parameters and material characteristics.
3. Particle microstructure and porosity have a measurable effect on the deposition
efficiency of cold sprayed materials. The presence of inter-particle pores can lead to lower
interfacial mixing and therefore weakening the inter-layer bonds as well as between the
deposit and substrate. The microstructure and porosity of the powder translate directly
to the deposit material and can directly influence the mechanical performance of the bulk
material[32].
4. Higher gas impurities increase the metal’s yield strength and thereby increase the critical
velocity[33, 34]. It is preferred to keep oxygen levels below 300 ppm, though the overall
measurement is a combination of internal, dissolved oxygen and the inherent surface
oxide layer. Finer powders, with a higher surface-to-volume ratio, will naturally have
higher oxygen content overall. The control of oxygen in these finer particle applications
becomes an equilibrium challenge between the particle size desired and the minimum
surface oxygen present.
5. The surface of a particle influences its flowability (see above), the deposition efficiency,
and coating properties[26, 30]. Particle surfaces with excess moisture, hydroxides and other contaminants, and extreme oxide layers will cause variation in flow through the system, lower DE, and poor coating strength due to less particle deformation and the
incorporation of contaminants, oxides, etc. in the coating. Powders for cold spray should
be processed, handled and stored to prevent contamination and surface reactions; where
possible they should also be dried and packaged under an inert atmosphere for optimal
quality and shelf life. Tantalum and niobium surface oxides are stable at room
temperature, however, additional care and preventative measures are recommended for
fine (<25 micron) and ultra-fine (<10 micron) particle sizes due to their high surface-tovolume ratio.
Global Advanced Metals Ta and Nb Powders
Global Advanced Metals (GAM) has a well-known history of producing high-quality Ta and Nb
products including flake and agglomerated powders for capacitors, and angular met-grade
powder as feed for mill products. GAM has applied the knowledge and capabilities used to
develop powders for the semiconductor and capacitor industries now to produce powders with
optimized and controlled particle size distributions and chemistry for cold spray applications. The micrographs in Figure 2 show examples of angular tantalum, tantalum-alloy, and niobium
powders developed for cold spray applications.

Figure 2. GAM angular powders designed for cold spray. Clockwise from top-left: 45-125µm
Ta, 10-25µm Ta, 10-25µm Ta-2.5W, and 15-40µm Nb.
Early cold spray development testing of GAM tantalum powders have demonstrated consistent
dense coatings with good bonding and low porosity. The powders used for these tests were
larger, spherical particles (A), larger angular particles (B), and smaller angular particles (C). Table
1 shows the powder attributes and Figure 3 shows the feed powders. Cold spray deposition was
performed by a collaborator to produce flat coupons, tensile bars, as well as coatings on interior
and exterior curved surfaces. Figure 4 shows macro photos of various part geometries. With only
preliminary parameters established, good bonding and low porosity were achieved as shown in
the SEM photos and EBSD images in Figure 5.
Table 1. Cold spray Ta powder attributes

1 Does not include gases.
2 N/A indicates powder did not flow through Hall funnel

Figure 3. Micrographs of powders A, B, and C used in cold spray testing (left to right).

Figure 4. Macro photos of Ta cold spray samples (dimensions are approximate), left to right:
50x50 mm flat coupon, 50 mm radius outer curve, 50 mm radius inner curve, 30mm diameter
cylinder.

Figure 5. SEM and matching EBSD images for (left to right): Powder A coupon section, Powder B
section, Powder C section. Growth direction is vertical in all cases.
Summary
As previous and emerging research have shown, careful control of powder properties is critical
for success in cold spray applications. Early testing has demonstrated that the positive results
seen in tantalum and niobium cold spray literature holds true for the high-quality powders
produced by GAM. GAM has extended well-established processing techniques commonly used
in the manufacturing of capacitor-grade and metallurgical-grade powders to the tantalum,
tantalum alloy, and niobium cold spray powders thus providing superior performance in the form
of consistent and controlled particle size distributions, excellent flow, and industry leading
chemistry. Further material development and cold spray testing have been performed and
additional results will be shared in future presentations and publications. GAM continues to
invest in the development and production of powders designed for cold spray and additive
manufacturing and thus will be well positioned to support the anticipated growth in this industry.
References
1 V. Champagne Jr, O. Ozdemir and A. Nardi, Practical Cold Spray, Springer, 2021.
2 S. Kuroda, 28 May 2021. [Online]. Available: File:Cold spray schematics.png. (2021, May 28). Wikimedia Commons, the free media repository. Retrieved Dec 11, 2021 from https://commons.wikimedia.org/w/index.php? title=File:Cold_spray_schematics.png&oldid=565605238.. [Accessed 11 12 2021].
3 T. Pelsoci, "ESTCP funded cold spray technology for DOD applications," 2015.
4 C. Munro, "Review of structural additive manufacturing for defence applications," Defence Research and Development Canada, 2018.
5 J. Conant, "Army researchers develop cold-spray system, transition to industry," Adelphi, 2015.
6 A. DeBiccari and J. Haynes.US Patent 8349396B2, 2013.
7 V. Champagne, A. Nardi and I. Nault, "Cold spray coatings for Cr and Ni plating replacement," 2019.
8 J. Haynes and J. Karthikeyan, "Cold spray copper application for upper stage rocket engine design," in ITSC, Orlando, 2003.
9 Materials Deposition, Cold Spray MIL-STD 3021, United States Dept. of Defense, 2008.
10 P. Leyman and V. Champagne, "Cold spray process development for the reclamation of the Apache helicopter mast support," Army Research Laboratory, 2009.
11 A. Parsi, J. Lareau, B. Gabriel and V. Champagne, "Cold spray coatings for prevention and mitigation of stress corrosion cracking," in CSAT, Worcester, 2012.
12 M. Showalter, "Cold Spray to Help Keep Turbines Spinning," 6 10 2021. [Online]. Available: https://www.pnnl.gov/news-media/cold-spray-help-keep-turbines-spinning.
13 P. Lu, "Corrosion resistant cold sprayed cladding for molten salt reactors," in PRiME, 2020.
14 E. Fusco, "The repair of hiatus hernia with tantalum mesh," Military Medicine, vol. 125, no. 3, pp. 189-190, 1960.
15 H. Tang, K. Yang, L. Jia, W. He, L. Yang and X. Zhang, "Tantalum bone implants printed by selective electron beam manufacturing (SEBM) and their clinical applications," JOM, pp. 1016-1021, 2020.
16 J. Tang, Z. Zhao, X. Cui, J. Wang and T. Xiong, "Microstructure and bioactivity of a cold sprayed rough/porous Ta coating on Ti6Al4V substrate," Sci. China: Technol. Sci., pp. 731-739, 2020.
17 S. Kumar and B. Stucker, "Development of a Co-Cr-Mo to Ta transition using LENS for orthopedic applications," in International Solid Freeform Fabrication Symposium, Austin, 2005.
18 ASM Materials for Medical Devices Database Committee, "Tantalum," in Materials and Coatings for Medical Devices: Cardiovascular, ASM International, 2009, pp. 124-129.
19 D. Hambling, "The U.S. Army wants some tank-busting silver bullets," Popular Mechanics, 20 1 2016.
20 S. Lee, J. Cox, D. Windover, M. Audino and D. Matson, "High-rate sputter-deposited Ta coatings on a steel liner for wear and erosion mitigation," Surf. Coat. Technol., vol. 149, 2001.
21 Committee on Armed Services House of Representatives, "National Defense Authorization Act for Fiscal Year 2020," 2020.
22 M. Trexler, V. Champagne and J. Kopchik, "Development of a novel erosion resistant coating system for use on rotorcraft blades," in AHS International 68th Annual Forum & Technology Display, Fort Worth, 2012.
23 PaintSquare News, "DOE Awards $1.1M for Cold Spray Research," 2021.
24 H. Koivuluoto, P. Vuoristo and J. Nakki, "Structure and corrosion behavior of cold-sprayed tantalum coatings," in ITSC, Las Vegas, 2009.
25 S. Paul and P. McNutt, "Corrosion performance of cold sprayed tantalum coatings," in CORROSION 2018, Phoenix, 2018.
26 B. Young, J. Heelan, S. Langan, M. Siopis, C. Walde and A. Birt, "Novel characterization techniques for additive manufacturing powder feedstock," Metals, 2021.
27 D. Helfritch and V. Champagne, "Optimal particle size for the cold spray process," in ITSC, Seattle, 2006.
28 O. Ozdemir, J. Conahan and S. Muftu, "Particle velocimetry, CFD, and the role of particle sphericity in cold spray," Coatings, 2020.
29 M. Rokni, S. Nutt, C. Widener, V. Champagne and R. Hrabe, "Review of relationship between particle deformation-coating microstructure and properties in high pressure cold spray," J. Therm. Spray Technol., pp. 1-40, 2017.
30 B. Sousa, M. Gleason, B. Haddad, V. Champagne Jr., A. Nardi and D. Cote, "Nanomechanical characterization for cold spray: from feedstock to consolidated material properties," Metals, vol. 10, 2020.
31 R. Huang and H. Fukanuma, "Study of the influence of particle velocity on adhesive strength of cold spray deposits," J. Therm. Spray Technol., pp. 541-549, 2011.
32 Y. Li, X. Luo and C. Li, "Dependency of deposition behavior, microstructure and properties of cold sprayed Cu on morphology and porosity of the powder," Surface and Coatings Technology, 2017.
33 L. Descurninges, L. Mingault, J. M., A. Nifa, L. Berthe, M. Boustie, T. Laguionie, L. Bianchi and K. Ogawa, "Influence of powder particle oxidation on the properties of cold-sprayed tantalum," in ITSC, Hamburg, 2011.
34 K. Murray, M. Kearns and A. Coleman. [Online]. Available: https://www.metalpowder.sandvik/cn/SysSiteAssets/metal-powder/products-applications/cold-spray/design-and-production-of-powders-tailored-to-cold-spraying.pdf. [Accessed 13 11 2012].
To access the full paper in a downloadable format, use the link below:
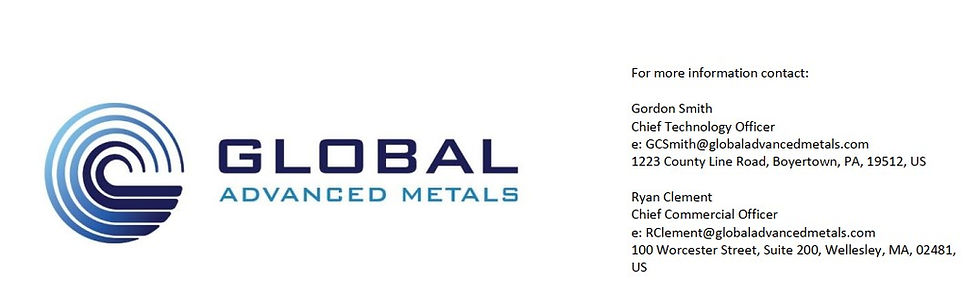
Comments