Tantalum: A Stable Supply Chain
- Global Advanced Metals
- Sep 13, 2022
- 4 min read
A stable, reliable, and responsible tantalum supply chain is critical to the supply of electronic components (e.g. capacitors, semiconductors) and other industrial forms (e.g. turbine blades, heat exchangers) for the automotive, aerospace, medical, defense, energy, and chemical processing industries. Until recently, the tantalum supply chain has experienced intermittent periods of stability and volatility.
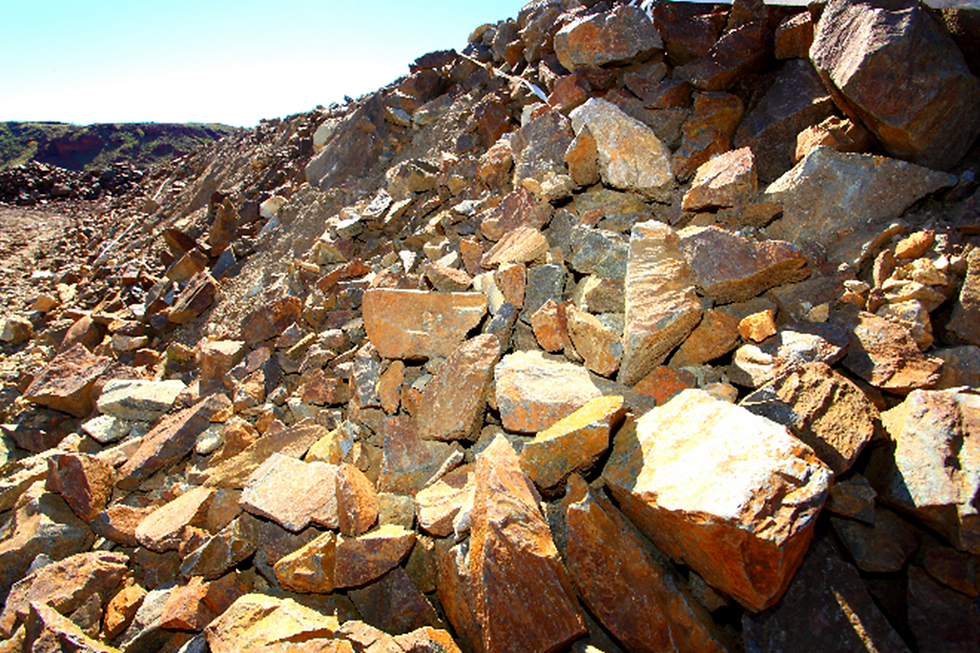
Over time, shifts in supply and demand dynamics have impacted the stability of the tantalum ore supply chain. Changes in concentration of mining methodology and geography, while having some positive economic effects, have also brought ethical concerns, regulatory necessities and questionable reliability. Electronic demand peaks caused real, and sometimes perceived, supply shortages. Those issues are now being resolved with strong supply solutions for today and well into the future, making the tantalum ore supply chain truly reliable and sustainable in support of all relevant industries.
Tantalum Supply: from Then to Now
Before the late 1970s tin mining was the primary source of tantalum concentrate (ore). Where present in Tin deposits, tantalum was removed and discarded as waste slag. This resulted in the accumulation of large quantities of waste tailings (tin slags) containing low grades of tantalum located primarily in Thailand and Malaysia. While now a small percentage of overall tantalum supply, synthetic tantalum concentrates from tin slags continue today as a tantalum supply from these same two countries.
In the 1980s the tantalum supply chain migrated away from tin slags and developed longer term industrial scale (often referred to as hard rock) tantalum mines as a primary source for ore concentrate(1). Western Australia was the largest source with other material coming from Brazil and Canada. The Western Australian hard rock tantalum sources were primarily from the Greenbushes and Wodgina mines, both still associated with tantalum ore supply today.
By early 1990s, the Western Australian mines invested to increase supply capability, but not fast enough to keep pace with rising demand from the mobile phone and internet bubble of 2000. The ensuing shortage caused the CEO of a well-known computer brand to exclaim on a financial broadcast "What is a tantalum capacitor and why can't I get one?"
The short answer was that a rapid supply increase was needed to meet the skyrocketing demand. Hard rock mine expansion is lengthy and costly and what little expansion occurred in the 1990’s fell short of the 2000 “bubble” market demand.
Artisanal scale mining, particularly in Central Africa, existed throughout much of this period but while less costly than hard rock mining was thwarted by ethical concerns. In the early 2010s, robust traceability mechanisms were implemented to assure users throughout the tantalum supply chain of chain of custody integrity. As these mechanisms matured, artisanal scale mining began to displace hard rock sources. Artisanal mining’s very nature of being simple and small-scale means it can be started or stopped quickly according to market conditions. However, the transience of this low-cost labor quickly becomes its disadvantage when independent subsistence-miners transition to mining of other minerals for better pay. This source of material can also be subject to manipulation by malign actors for personal gain, thus causing further supply disruption.
Tantalum Supply: A Stable Future
To address the need for responsible sourcing, the tantalum, tungsten, tin, and gold (aka 3TG) industries implemented the Conflict Free Sourcing Initiative (CFSI), known today as the Responsible Minerals Initiative (RMI). The RMI, founded in 2008, created a comprehensive set of tools and processes to enable the credible implementation of responsible and ethical mining and trade practices in the Central Africa tantalum supply chain.

In December 2010, the Global Advanced Metals (GAM) tantalum processing plants in the USA and Japan were the first of any metal type to be audited and declared “Conflict-Free” by CFSI. Since then, over 40 companies that participate in the tantalum supply chain are audited annually and maintain compliance to the regulatory and industry conflict-free standards.
Today, the rapidly growing market for electric vehicles is bringing a new age of lithium mining which provides additional stability to tantalum sourcing. Lithium and tantalum frequently co-exist in hard rock mines in Western Australia, South America, Africa, and elsewhere. Global lithium resources of all sources (brine and mineral concentrate) are estimated to be almost 400 million tons(2). Tantalum as a co-product is found in the lithium mineral concentrate source. Current estimated global resources of tantalum co-product are over 37 million tons(3).
This tantalum co-product is extracted with relatively minimal incremental environmental impact, predictable economics, and rising volumes. In fact, recovering the tantalum as a co-product from lithium hard rock mining should be viewed as a “green” technology as the tantalum recovered would otherwise be disposed of as waste. The long term lithium demand outlook ultimately provides additional tantalum confidence in addition to ongoing artisanal and hard rock mining, tin slag sourcing, and tantalum recycling for a long period of stable and reliable tantalum supply.
Over the past 70 years of use across various applications, the tantalum industry has developed into a multi-sourced, responsible, and stable supply chain. The 2020s have ushered in a new era for tantalum market stability. Current tantalum demand is estimated to be 2,300 tons with a 3% to 5% annual growth rate through 2029(4). Tantalum ore supply is stronger than ever and ready to support the increasing demand from tantalum capacitor makers, semiconductor manufacturers, aerospace, additive manufacturing, other industries and new applications for tomorrow.
1. Roskill Tantalum Market Update, Analysis and Outlook, Roskill Information Services Ltd., London England, March 1995
2. Lithium Extractive Cost Model Service, Roskill Information Services Ltd., London England, June 2021
3. Niobium and Tantalum: Chapter M of Critical Mineral Resources of the United States - Economic and Environmental Geology and Prospects for Future Supply, Klaus J. Schulz, Nadine M. Piatak, and John F. Papp, U.S. Geological Survey, Reston, Virginia, 2017
4. Tantalum: Outlook to 2029, Roskill Information Services Ltd., London England, April 2020
コメント