Safety & Handling Evaluation for Solvus Global Cold Sprayable Metal & CERMET Powders
- Solvus Global
- May 8, 2020
- 12 min read
Prepared for the U.S. Army Research Laboratory
May 08, 2020
Solvus Global, LLC.
INTRODUCTION
Dust Hazard Analysis is vital for many industries from, grain mills to plastics producers. Fine particulates have the potential to auto-ignite into an explosion if dispersed in sufficient concentration in the presence of an ignition source and oxidizer [1][2][3]. There is frequent concern in the cold spray industry over the use of fine metal particulates, which are commonly considered to be a fuel if exposed to an ignition source.
At Solvus Global (SG), we engineer our powders to be as non-flammable, non-combustible, and as safe as possible with the safety of our consumers always at the forefront of our innovation.
The traditional nature of fine metal powder with its high surface-area–to–volume ratio is the typical driver for combustibility. Processing, moving, and transporting these materials are often limiting factors for users. In order to support rapid adoption of cold spray into Army Research & Repair Depots, Solvus Global (SG) has worked with Exponent, a world-renowned testing lab, to evaluate each of the powder products offered and ensure that safe handling and operation in a cold spray repair and manufacturing center can be achieved. The discussion below will provide information on the testing procedures and the significance of those tests in helping to inform and support the Authorities Having Jurisdiction (AHJ’s), who are ultimately responsible for approving acceptable handling and use procedures. Furthermore, Solvus Global’s powder materials are discussed on their explosion characteristics.
DUST HAZARD DESCRIPTORS
EXPLOSION SEVERITY
Safety process design engineers typically will use Kst and PMax in order to build explosion mitigation, explosion venting, and proper housekeeping systems [4]. Kst, as defined by OSHA, is the dust deflagration index of a material. It measures the relative explosion severity compared to other materials. Table 1 below provides an example of Kst for some common items in processing facilities that have the likelihood of a dust explosion. This table was taken from an OSHA-published document [4]. Most notable in this table is aluminum powder, which is a generalized value and not representative of Solvus’ materials. Kst is not meant to be taken as the ‘true’ explosivity of a material but is a good indicator for dust explosion behavior. Kst is determined via the testing methods described in ASTM E1266 and can be converted to PMax.
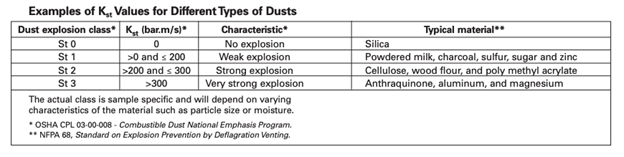
Similarly, PMax is used as an indicator for the relative danger of a dust explosion. As the variable implies, it is measuring the maximum pressure that can be generated in a defined and enclosed volume or space with a specified amount of ignitable material [5]. This is an important value in determining the dangers of a powder in an enclosed environment such as a freight truck bed, duct work, or a flammables cabinet. Another value that can be determined during PMax testing is dP/dt. This value is described as the change in pressure over time during an explosion.
IGNITION PROPERTIES
The important ignition properties of dust explosions are Minimum Explosive Concentration (MEC) and Minimum Ignition Energy (MIE). MEC is the measure of the minimum amount of material required to create an explosion when dispersed in air [4]. MIE is the minimum amount of energy in order to combust a dispersed dust cloud of material. This energy can come in the form of a spark or a heat source. As a corollary to MIE, Minimum Ignition Temperature (MIT), is the minimum temperature required to ignite a dust cloud or layer [6]. Table 38: and Table 3 show a short summary of these terms, the significance, and the source of standard.
UNITED NATIONS (UN) RECOMMENDATIONS ON THE TRANSPORT OF DANGEROUS GOODS
In addition to the properties described above, the United States Department of Transportation as well as local Fire Departments defer to the UN Recommendations for ‘Flammable Solid Testing’. The ones of most importance to this document are UN 4.1 through UN 4.3 which determine Solid Flammability, Self-Heating Materials, and Flammable Gas Emission in Contact with Water, respectively.

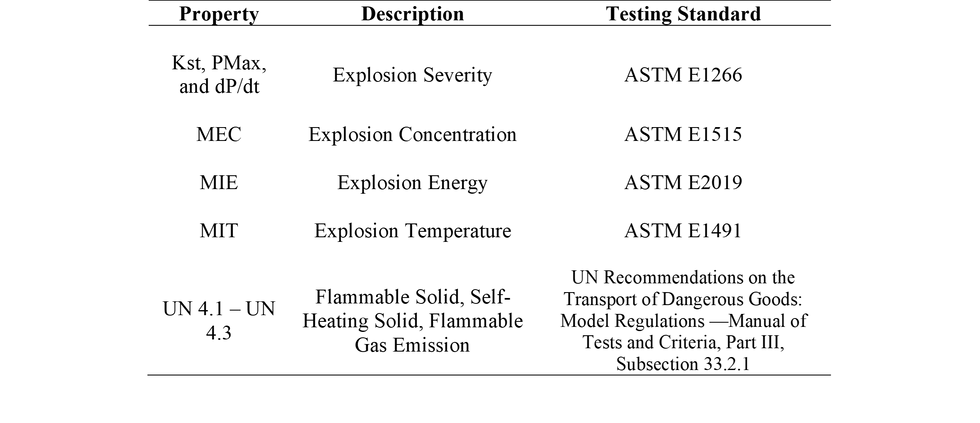
TESTS OF INTEREST
PRIMARY TESTS
The following tests are required for a Dust Hazard Analysis:
Kst, PMax, and dP/dt
MEC
MIE
MIT (or MAIT)
UN 4.1 – UN 4.3 – Transportation of Dangerous Goods
Metrics of interest include Kst, obtained via ASTM E1266. This value is calculated by measuring PMax, dP/dt, and volume of the igniting vessel where the highest rate of change is at max using the following equation:

Additional tests for MEC, MIE, and MIT will be conducted using guidelines from ASTM E1515, ASTM E2019, and ASTM E1491, respectively. Regarding MEC, the Pressure Ratio (PR) is calculated with equation 2 below. Per ASTM E1515 and the instruction manual on the testing chamber, pressure adjustments are made using this formula to account for pressure from the ignitor and walls of the vessel. The MEC is defined as the lowest concentration where the Pressure Ratio ≥ 2.0.

MIE requires the use of two formulas in order to account for the energy generated by the ignitor and capacitors used in that ignitor. W is the capacitor stored ignition energy, C is the capacitance of the discharge capacitor, V1 is the voltage on the capacitor when charged, and V2 is the voltage on the capacitor after discharge. The subsequent equation interpolates the MIE based on the observed results for maximum energy where ignition was not observed and minimum energy when ignition was observed in equation 4.

Additional testing for UN Classification can be conducted to determine hazard classifications of Division 4.1, 4.2, or 4.3 per the United Nations Recommendations on the Transport of Dangerous Goods (2009).
TESTING SETUP
Kst, PMax, and dP/dt
The explosion severity variables Kst, PMax, and dP/dt were evaluated using a Kühner 20-Liter Combustion Chamber with two 5 kJ igniters (10 kJ total). Testing is conducted in accordance with ASTM E1226 – 12a, Standard Test Method for Explosibility of Dust Clouds. Materials conformed to ASTM recommendations of moisture content below 5% with at least 95% of particles by mass below 200 mesh (75 micron). In general, the max pressure and explosion severity index will increase with decreasing particle size.
MEC
MEC also employs the same testing chamber as in Figure 1. MEC testing is conducted in accordance with ASTM E1515-07 Standard Test Method for Minimum Explosible Concentration of Combustible Dusts. The ignition source is from a 2.5 kJ Sobbe Igniter.
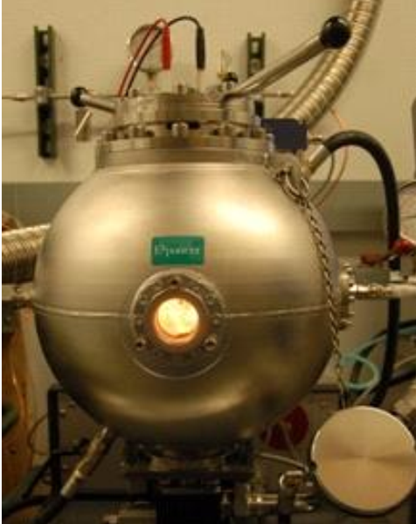
MIE
MIE was tested with the Kühner MIKE3 MIE Test Apparatus shown in Figure 2. A variable spark igniter was used for ignition with an inductance of 1 mH. MIE follows ASTM E2019 for Standard Test Method for Minimum Ignition Energy of a Dust Cloud in Air. MIE uses the same moisture and particle sizing requirements as MEC.

MIT
MIT (or Minimum Autoignition Temperature) employs the 0.35-L BAM Oven in accordance with ASTM E1491 – 06 Standard Test Method for Minimum Autoignition Temperature of Dust Clouds.
UN 4.1 – UN 4.3 – TRANSPORTATION OF DANGEROUS GOODS

UN testing for class 4.1 through 4.3 is conducted as follows in this section. An unbroken strip of powder material 10mm in height, 20mm in width, and 200mm in length is exposed to a torch flame in excess of 1000°C for 5 minutes. If a fire propagates through the strip from the origin the material is considered a readily combustible solid per UN 4.1 from Transport of Dangerous Goods: Model Regulations – Manual of Tests and Criteria, Part III, Subsection 33.2.1.
UN 4.2 Test Method for Self-Heating Substances dictates that a sample is placed in a 25mm or 100mm wire mesh cube and heated in open atmosphere to 100°C, 120°C, or 140°C. A positive result occurs (substance is self-heating) if spontaneous ignition occurs or the sample exceeds the oven temperature by 60°C during the 24 hours of testing.
UN 4.3 Testing taken from Transport of Dangerous Goods: Model Regulations – Manual of Tests and Criteria, Part III, Subsection 33.24.1 dictates that water is added to target material at room temperature and the emission rate of gasses is observed.
SUMMARY OF INTENDED TESTING
SUMMARY
The most salient point from this document is to understand the difference between Explosion Severity (ASTM Testing) and Solid Flammability (UN Testing). The former studies how severe of an explosion is caused and what minimums (material, temperature, or ignition energy) are required to induce an explosion.
The latter studies whether a material (non-dispersed) is a flammable solid, self-heating, or emits flammable gas in contact with water. Both studies, when coupled together, give a more complete description for use, safety, storage, and shipment of the materials in question.
TESTING RESULTS
ALUMINUM METAL POWDER
INTRODUCTION
Solvus Global evaluated its thermally processed aluminum product line – Aluminum Alloys (AL2024, AL6061, AL7050, and AL7075) with 3rd party testing facility Exponent located in Natick, MA. The materials written above were produced at Solvus Global’s facility in Worcester, MA (as is standard for the materials) and shipped to Exponent. Exponent performed all tests per the appropriate standards and methods as described by UN and ASTM requirements. This work was supported by the US Army Research Lab. From here on in, the material names will be referenced by their constituent instead of the Solvus Global names for consistency, such as ‘AL2024’ instead of ‘SAAM – AL2024 – G1H2’.
RESULTS IN WHOLE
Results in the whole and unedited form from the testing facility are accompanied with this document for clarity and transparency. It must be noted that extensive testing was conducted and represents Solvus Global powders in the processed and packaged (i.e. ready to ship) condition. This does not apply to other materials from alternative vendors. Original documentation produced by Exponent can be released by request. Reformatted data is contained within this document in Table 4.

DISCUSSION
Recalling the sample data cited from OSHA guidelines in Table 1, a Kst between 0 and 200 (bar*m)/s is classified as a ‘Weak Explosion’ on the order of charcoal, sugar, zinc, or sulfur explosions. Aluminum powder on this same table is 300 or greater in the class of ‘Very Strong Explosion’. The testing conducted on Solvus Global’s material by Exponent is between 72 and 96 (bar*m)/s and can be found in Table 4. Since PMax is a volume dependent variable, KST is used to normalize this value to volume in order to better, but not completely, compare severity. Although Solvus Global’s material qualifies as a ‘Weak Explosion’ caution must still be undertaken to ensure safety for operators and users.
SAAM – Aluminum 2024, 6061, 7050, and 7075 have very comparable MEC, MIE, and MAT values. Recall that the higher the value of each of these variables, the safer the material is. A higher concentration of material, higher ignition energy, and a higher autoignition temperature means that much more effort is needed to induce an explosion. Referring to Table 5 and Table 6, an excerpt of NFPA 484 showing the Explosibility Properties of Metals, aluminum can be seen with a variety of entries [7]. SAAM materials have a median diameter of approximately 33-41 microns. The aluminum powder with a diameter of less than 44 microns would be most comparable in this situation. NFPA 484 suggests that a generic aluminum powder has an MIE and MEC of 50 mJ and 45 g/m3 respectively, with no acknowledgement of composition. A larger MEC means more material is required in order to have an explosion when in dust cloud form. SAAM materials have a larger MEC than NFPA 484 values for a comparable item. Solvus Global’s AL2024, AL6061, and AL7075 have significantly larger interpolated MIE values than NFPA 484 values, averaging 363 mJ compared to the NFPA value of 50 mJ. Having a larger MIE means much more energy is needed (spark or other ignition source) in order to induce an explosion. Although AL7050 has a relatively lower MIE at 82 mJ, it is still much higher than the NFPA aluminum values for a comparable median particle size. The lower MIE of AL7050 is likely due to the relative concentration of finer particles compared to other SG aluminum alloys. SG’s AL7050 has an upper limit of 2% by weight of particles below 10 microns (with an average of 1% below 10 microns) whereas SG’s other alloys have an upper limit of 1% below microns (where the average is about 0.2% below 10 microns). In either case, it is more difficult to induce an explosion in SG aluminum materials.
All the aluminum materials discussed have a similar MAT value of about 600°C, which is also similar to the bulk melting temperature of aluminum alloys between 600°C and 660°C. Although the MAT of these powders is close to that of bulk material, considerable care and safety should still be taken if operating temperatures ever reach these temperatures. However, since typical operating temperatures are not close to melting, having an MAT close to that of the melting temperature provides a larger range of safer operation.
These materials also qualify as NOT readily flammable solids and NON-self-heating materials per UN 4.1 and UN 4.2. Regarding UN 4.3, Solvus Global’s aluminum products do NOT emit flammable gasses in contact with water, except for AL7050. AL7050, when in contact with water, can emit hydrogen gas with the following reactions as shown in equations 5 – 7 [1], [8].

All these reactions are thermodynamically favorable from room temperature up to and past the melting point of bulk aluminum. All reactions are also highly exothermic [1]. UN 4.3 testing found that, when in contact with water, AL7050 produces an estimated maximum of 3.67 liters/kg/min. Although any production of flammable gasses is a concern, hydrogen gas is already used in numerous manufacturing and industrial settings such as welding and even fuel for vehicles [9].
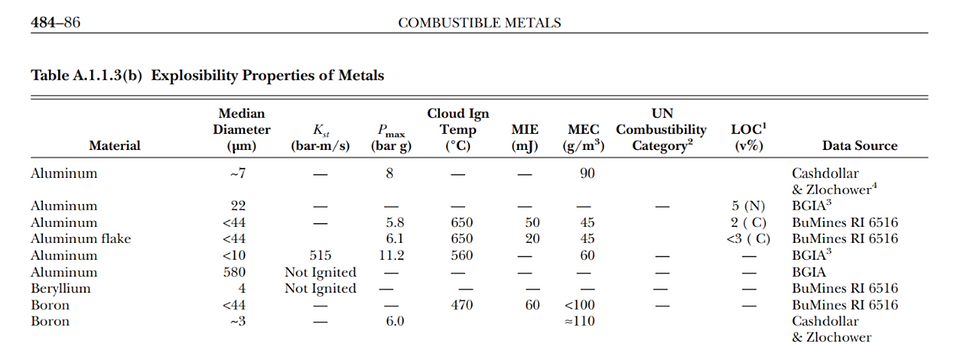
Due to hydrogen’s molecular properties, it is significantly lighter than air, dissipates rapidly if released, and is non-toxic [9]. These properties have made it safer to handle hydrogen gas than most commonly used fuels [9].
In summary, all of Solvus Global’s SAAM products are significantly lower in explosion severity and explosion likelihood compared to OSHA’s evaluation of aluminum powder and are not readily flammable materials. Healthy caution must still be taken to ensure safety and good-housekeeping practices. These practices include, but are not limited to, electrostatic dissipating personal protective equipment, removing ignition sources, minimizing use of water in operational locations, and fume management. These practices are the same for any activity involving the use of any powder, such as reducing the formation of dust clouds, avoiding introduction of water, and using appropriate PPE.
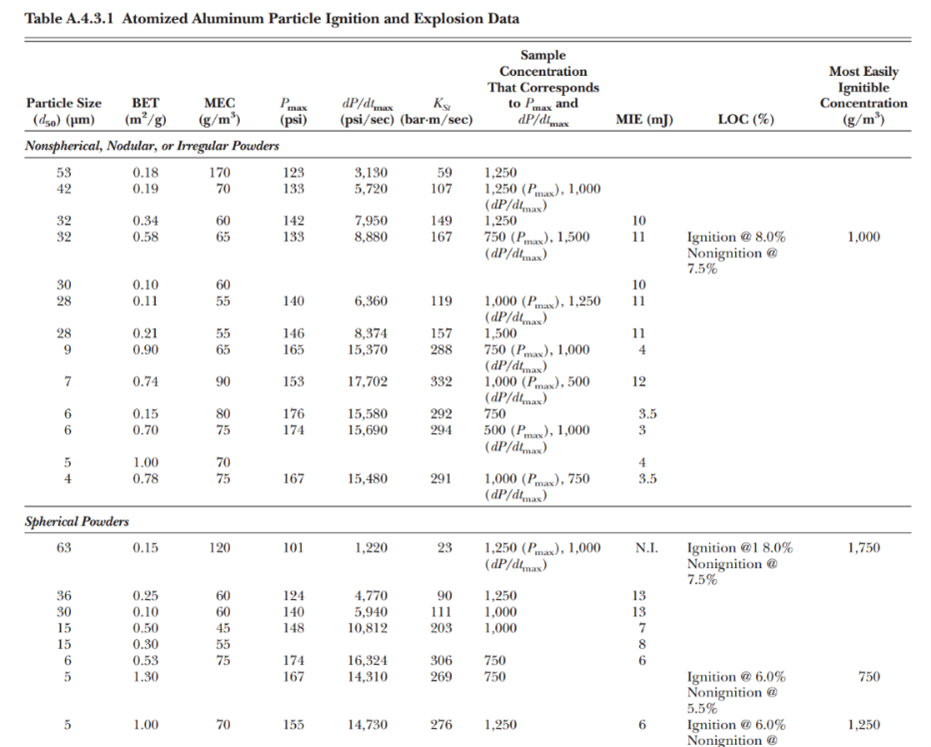
WIP – WEAR & IMPACT RESISTANT CHROME & NICKEL BASED MATERIALS
INTRODUCTION
Solvus Global does not thermally, mechanically, or chemically alter the primary constituents of the WIP – Chrome materials (C1, C2, and BC1) when used or sold for use. By contrast, SG’s SAAM materials are processed in a confidential environment for time and temperature that has the potential to alter the structure of those constituents. The only operation that is conducted on these WIP materials leaves constituent phases completely unaltered. Further, as the primary constituents are non-reactive to one another, Solvus Global recommends using the raw material provider safety data sheets, which are included below for completeness. In support of the vendor(s’) explosion and flammability testing, WIP-C1 was tested. Due to the extremely close compositions and identical ingredients across the WIP-Chrome materials, one type of material was sufficient. Compositions of C1, C2, and BC1 can be found in Table 40.
RESULTS IN WHOLE
Results in the whole and unedited form from the testing facility are accompanied with this document for clarity and transparency. It must be noted that extensive testing was conducted and represents Solvus Global powders in the processed and packaged (i.e. ready to ship) condition. This does not apply to other materials from alternative vendors. Original documentation produced by Exponent can be released by request. Reformatted data is contained within this document in Table 7.

DISCUSSION
The vendor from which SG sources the constituent materials ensures that they are in fact non-flammable solids via their own testing. This data is obtained from the vendor’s own Safety Data Sheets, which are in compliance with the Department of Transportation for shipment. As seen in Section 14, Figure 4, the Safety Data Sheets from the vendor(s) show no shipping hazards. This section is identical for the constituent materials. This section denotes the flammability of solids and are shown as non-flammable solids. These figures are taken directly from the vendor(s’) Safety Data Sheets to support this argument. As the materials are blended as described, Table 40 describes the nominal compositions of the WIP materials.
Based on testing that was conducted and reasoning that the composition difference between WIP-C1, C2, and BC1 are negligible, no explosibility was found in the form tested. A significant amount of energy is required (over 1000 mJ) to induce an explosion and is outside of the testing range for the system used. WIP-C1, and subsequently C2 and BC1, are NOT readily flammable solids nor do they react in contact with water.

APPENDIX
ALUMINUM RESULTS IN WHOLE
AL2024 – G1H2
EXPLOSION SEVERITY CHARACTERISTICS: Kst, PMax, and dP/dt




IGNITION PROPERTIES: MIE, MEC, MIT (MAIT)



UN CLASSIFICATION TESTING & DOT DANGEROUS GOODS TESTING

AL6061 – G1H1
EXPLOSION SEVERITY CHARACTERISTICS: Kst, PMax, and dP/dt
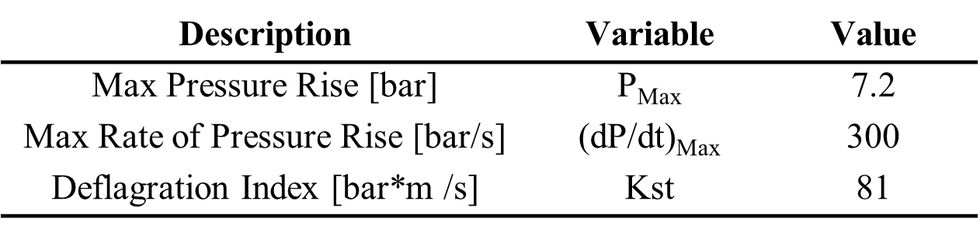

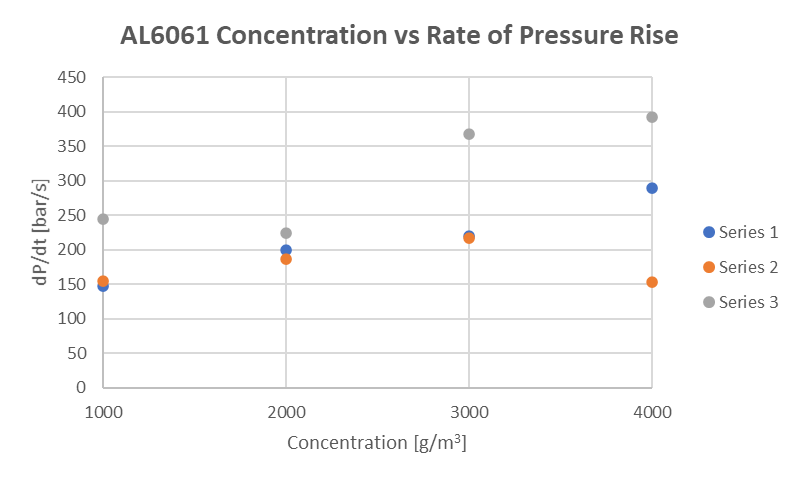

IGNITION PROPERTIES: MIE, MEC, MIT (MAIT)
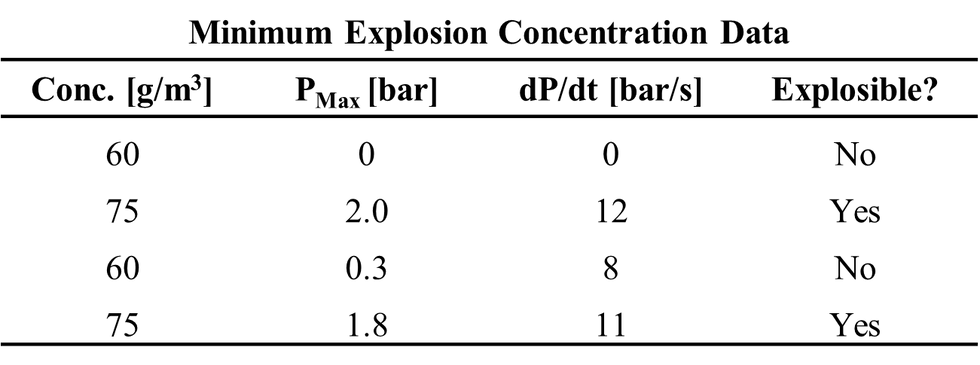


UN CLASSIFICATION TESTING & DOT DANGEROUS GOODS TESTING
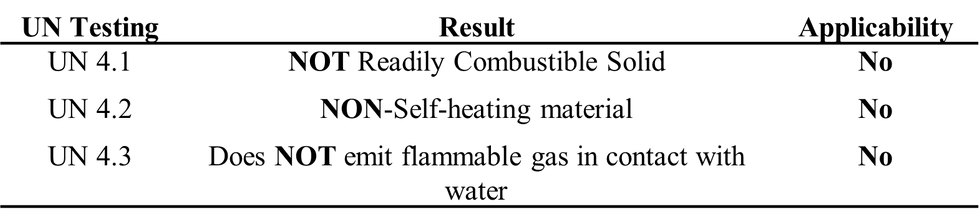
AL7050 – G1H3
EXPLOSION SEVERITY CHARACTERISTICS: Kst, PMax, and dP/dt
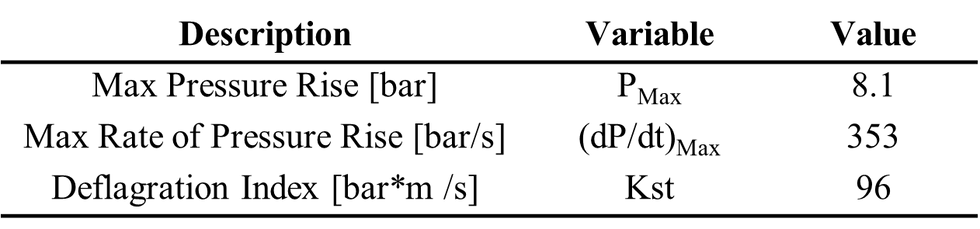
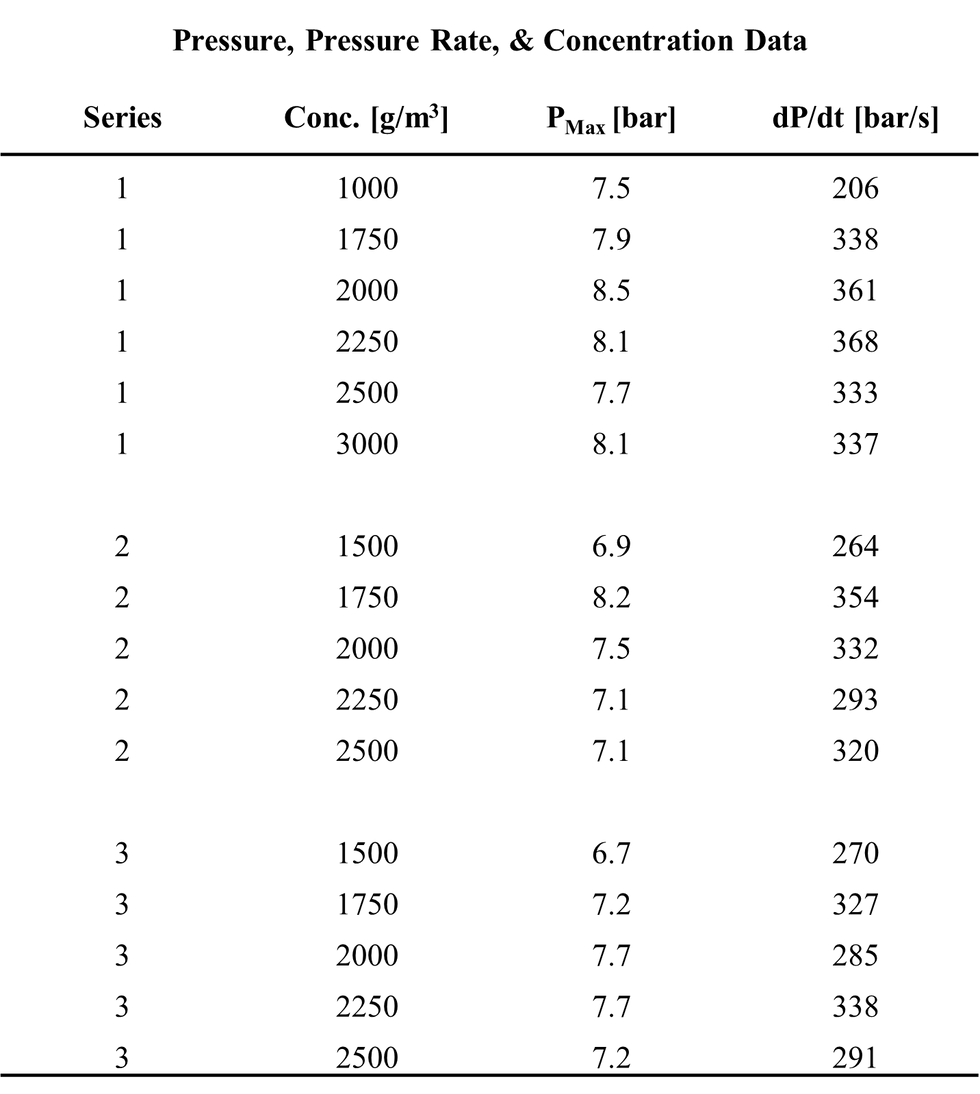


IGNITION PROPERTIES: MIE, MEC, MIT (MAIT)



UN CLASSIFICATION TESTING & DOT DANGEROUS GOODS TESTING





IGNITION PROPERTIES: MIE, MEC, MIT (MAIT)
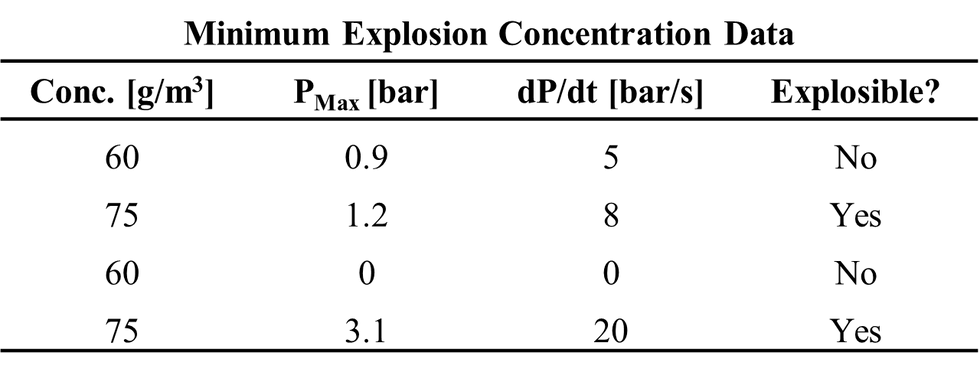
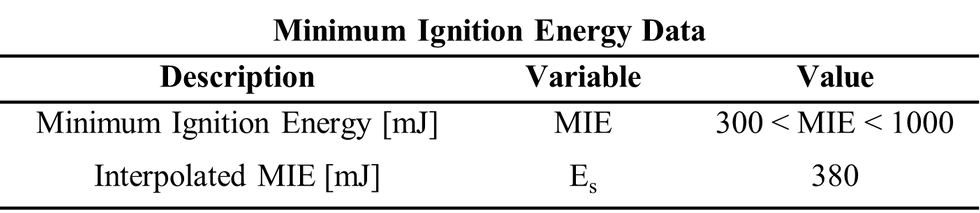
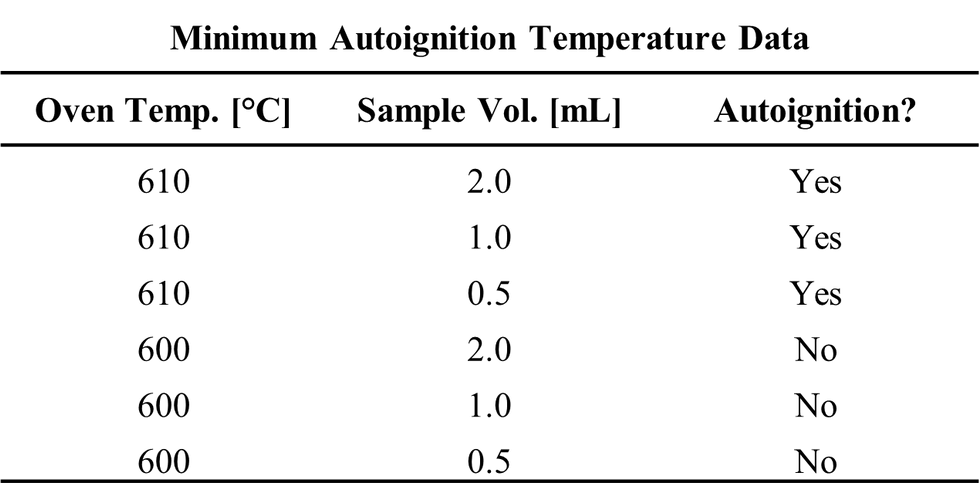
UN CLASSIFICATION TESTING & DOT DANGEROUS GOODS TESTING
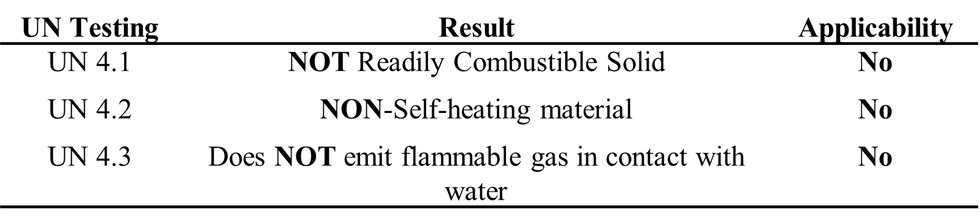
WIP CHROME RESULTS IN WHOLE
EXPLOSION SEVERITY CHARACTERISTICS: Kst, PMax, and dP/dt
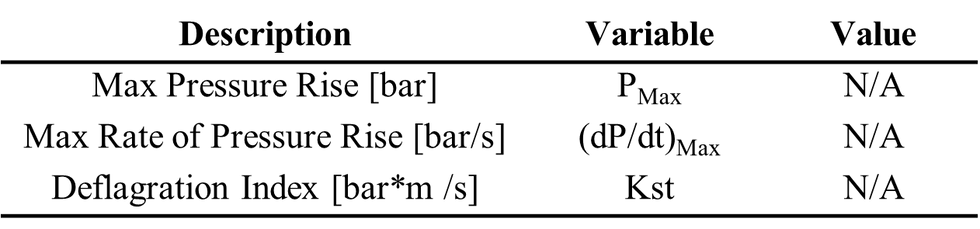

IGNITION PROPERTIES: MIE, MEC, MIT (MAIT)

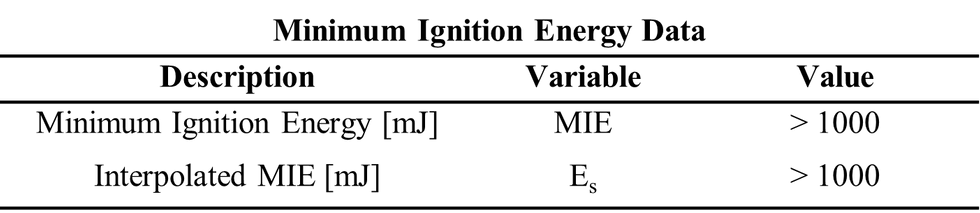

UN CLASSIFICATION TESTING & DOT DANGEROUS GOODS TESTING

SUMMARY OF PROPERTIES
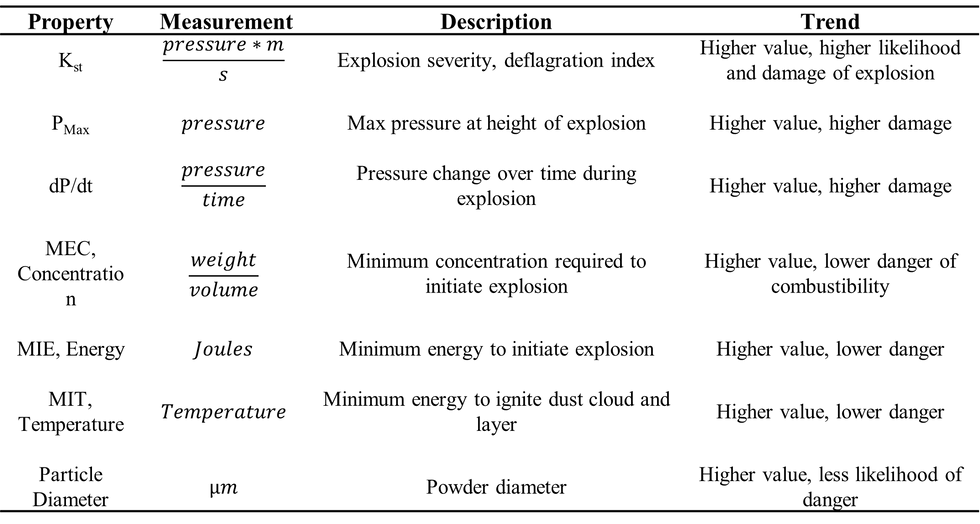
SUMMARY OF TESTING AND METHODS
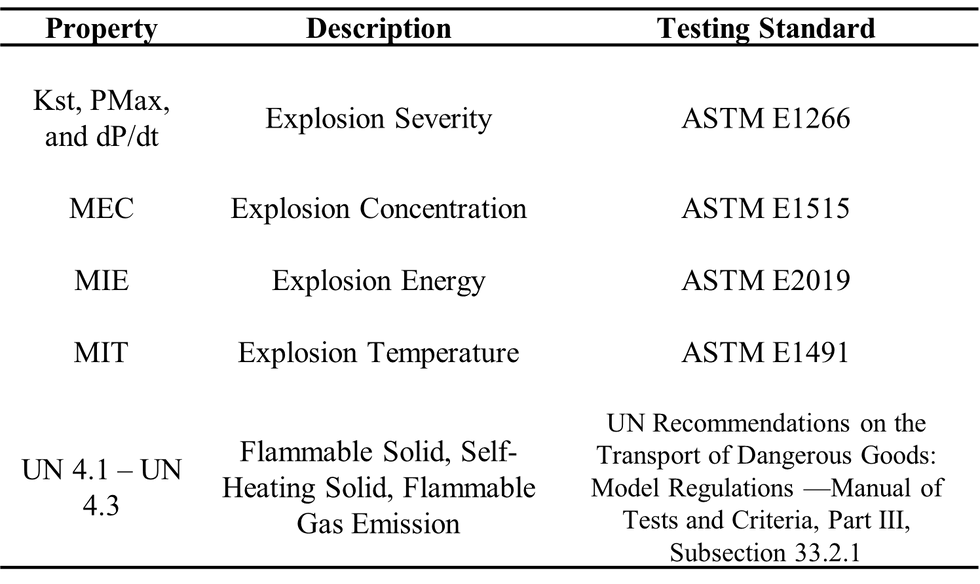
COMPOSITIONS OF WIP MATERIALS
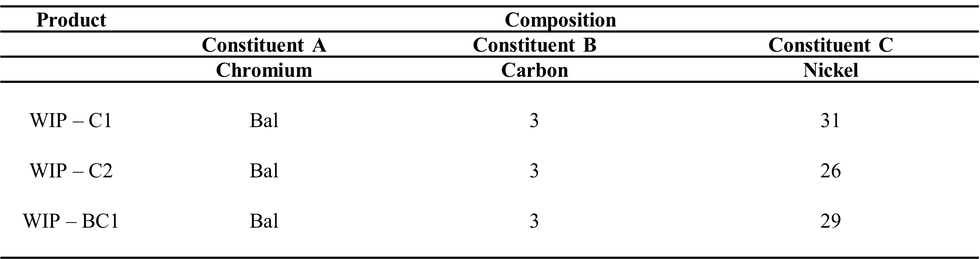
CITATIONS
[1] J. Petrovic and G. Thomas, “Reaction of aluminum with water to produce hydrogen,” 2008.
[2] G. K. Gomma and M. H. Wahdan, “Schiff bases as corrosion inhibitors for aluminium in hydrochloric acid solution,” Mater. Chem. Phys., vol. 39, no. 3, pp. 209–213, Jan. 1995, doi: 10.1016/0254-0584(94)01436-K.
[3] Fauske.com, “Kst and Pmax Testing For Combustible Dust: Who or What Are They?” [Online]. Available: https://www.fauske.com/blog/kst-and-pmax-tests-for-combustible-dust. [Accessed: 04-Nov-2019].
[4] Occupational Safety and Health Administration, “Hazard Communication Guidance for Combustible Dusts,” Washington, DC, 2009.
[5] “KST, PMAX, MIE… What Does It All Mean for Your Combustible Dust?” [Online]. Available: https://www.isystemsweb.com/combustible-dust/. [Accessed: 04-Nov-2019].
[6] “A Practical Guide to 5 Important Properties of Combustible Dusts.” [Online]. Available: https://www.hallam-ics.com/blog/a-practical-guide-to-5-important-properties-of-combustible-dusts. [Accessed: 04-Nov-2019].
[7] NFPA Standard 484, Standard for Combustible Metals. 2015.
[8] Y. Wang, K. Xu, and L. Li, “Inhibition of the reaction between aluminium dust and water based on the HIM,” RSC Adv., vol. 7, no. 53, pp. 33327–33334, 2017, doi: 10.1039/c7ra04787h.
[9] “Safe Use of Hydrogen | Department of Energy.” [Online]. Available: https://www.energy.gov/eere/fuelcells/safe-use-hydrogen. [Accessed: 10-Apr-2020].
Contact
Dr. Sean Kelly
Solvus Global Co-Founder & Chief Operations Officer
sean.kelly@solvusglobal.com
104 Prescott Street, Worcester, MA, 01605
(508) 373-2750
To view the Safety & Handling Evaluation for Solvus Global Cold Sprayable Metal & CERMET Powders document in its entirety, please download the pdf file below. For more information on Solvus Global, visit their website: www.solvusglobal.com
Comments