High-Purity Spherical Tantalum Powder for Additive Manufacturing
- Global Advanced Metals
- Dec 13, 2023
- 12 min read
A. Calvin and M. Osborne
Global Advanced Metals, Boyertown, PA
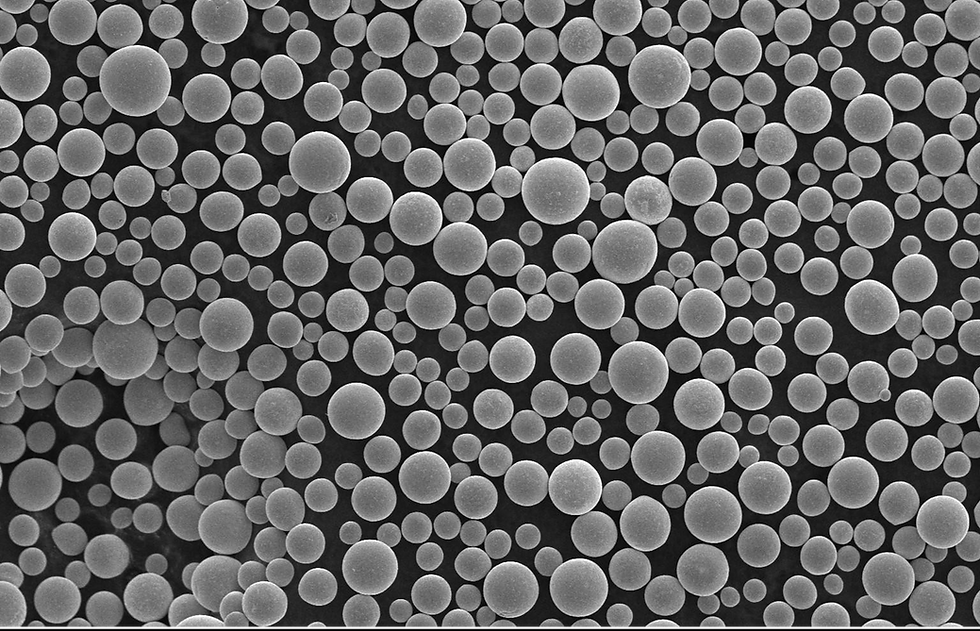
Abstract
New developments and innovations in the energy, defense, and medical sectors require advanced materials to meet emerging applications. Refractory metals, such as tantalum and tantalum alloys, are playing a pivotal role in meeting these new challenges due to their high-temperature performance, biocompatibility, and ductility. To achieve the highest performance possible, purity and quality must be maintained from raw material to the final product. Through careful manufacturing controls, high-purity materials can be consistently produced to ensure success in the product applications. Additive manufacturing reduces material scrap and waste; therefore lowering the cost and barrier of entry for these alloys, improving the buy-to-fly ratio for many aerospace applications. This presentation will review and highlight high-purity powders developed for a variety of additive manufacturing (AM) techniques such as laser or electron beam powder bed fusion (LPBF, EB-PBF)and directed energy deposition (DED). By controlling impurities such as oxygen, nitrogen, and carbon, it is possible for AM-grade tantalum to achieve mechanical performance on par with wrought materials.
Introduction
Tantalum (Ta) is a dense and ductile refractory metal used in applications which require its thermal performance, chemical resistance, or bio-compatibility [1, 2]. Additive manufacturing lowers the cost of utilization for refractory metals by minimizing material waste and machining time. It allows the creation of novel components in a wide-range of applications that can capitalize on the material properties of tantalum and its alloys, particularly in aerospace and medical. The applications in these industries are exacting, and to achieve the desired performance from printed components the consistency and purity of the powder is paramount. Oxygen and nitrogen act as interstitial elements in tantalum impacting the ductility and mechanical properties of the final material; therefore, it is important to monitor, limit and control these elements during powder manufacture. In addition to the elemental concerns, particle size distribution (PSD), particle shape, powder flow, powder packing, and cleanliness will all have an impact on part and material quality. Achieving and maintaining high quality and high purity material is challenging and it requires careful considerations and engineering controls for every operation from ore refinement to powder storage. Upon exposure to air at ambient conditions, tantalum will form an oxide layer of approximately 2-3 nm which passivates the surface [3]. For a typical powder used for LPBF (15-45 µm), this natural oxide layer, along with dissolved oxygen in the particle body, corresponds to an oxygen level of ~100 ppm, thus giving an immutable target for purification. With a +/-10% repeatability for combustion oxygen measurements and an upper control limit of three sigma for a typical production process, a high-quality tantalum powder for additive manufacturing should have oxygen in the range of 150-200 ppm.
The level of oxygen in an additive manufacturing tantalum powder is key variable in enabling the optimization of mechanical properties in a component or device. As previously mentioned, oxygen behaves as an interstitial element in tantalum, reducing ductility and increasing tensile strength. Figure 1 shows oxygen content and corresponding mechanical performance for both LPBF printed and wrought material.
Similar trends are evident between printed and wrought tantalum, namely elongation at break decreases and tensile strength increases proportionally with oxygen content. Optimizing ductility and strength is a desirable and unique trait being investigated and exploited for aerospace and medical devices. By using an AM powder with the lowest starting oxygen, it permits users to adjust oxygen content, balancing the yield or ultimate tensile strength with elongation. Having a tantalum powder at 250ppm or greater limits the potential applications and usage of the printed material. At oxygen less than 200 ppm, LPBF parts have elongation of 40% or more, which is a key material trait and allows for users to maximize material usability.
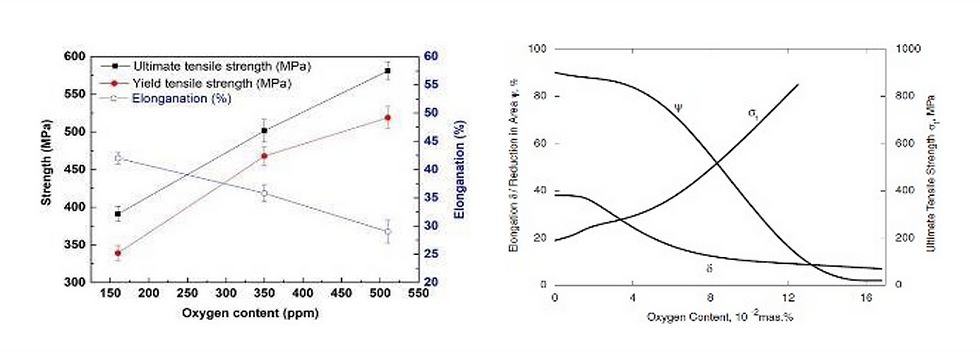
By the nature of printing, the AM powders are expected to be reused, reducing the total cost of implementation. Reusable powders are especially important for materials such as tantalum that have a base cost greater than most common alloys. Metal powders readily absorb oxygen at elevated temperatures, and during AM printing, powder that is adjacent to the melt path or solidified into the part will see an increase in oxygen content.For tantalum, oxygen increase during AM will send the mechanical properties along the trend lines shown in Figure 1. It is important to lower oxygen for the starting material as much as possible to account for the increases that will occur during the printing process. Research has shown that tantalum powder will absorb oxygen as usage increases, but this is very dependent on the printing technique [17].
Figure 2 highlights the increase in oxygen when Ta powder is reused for electron beam (EB-PBF) printing.
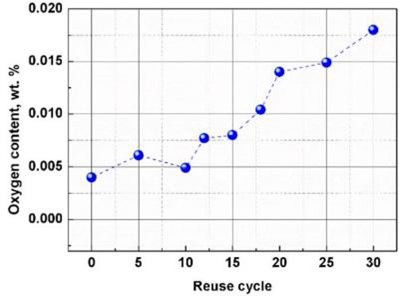
Beyond absorbed oxygen within powder particles, oxygen also increases from extremely high surface area ultra-fine particles generated during AM processing. The ultra-fine particles have much higher surface area to volume ratios causing higher natural oxide per mass of material.By maintaining powder cleanliness, i.e., screening out fine particulates and oxides between builds, the increase in oxygen with reuse can be moderated. In addition to printing induced changes in oxygen content, there will also be changes to particle morphology, particle size distribution, and the surface condition of the particles [6]. Particle size and shape directly influence spreadability and packing in a powder bed printer and it is important to have consistent properties lot-to-lot and also throughout the useful life of the powder. The shape and consistency will dictate how well a powder flows, packs, accelerates, and densifies. For powder bed applications, particles should be highly spherical with few satellites, dry, and free of static charge. During printing operations particles may partially join,forming a non-flowing composite body which will impact the condition of the material, the particle size distribution, and the print quality. The surface condition of the particles can change during printing due to metal vapors condensing on the powder particles. This condensed material alters the surface roughness of the powder, slows flow and reduces open area within the powder. Monitoring the powder morphology and particle size distribution between builds with periodic screening of satellite agglomerates helps ensure consistent print performance.
Regardless of printing technique, the powder must be free from environmental contamination or foreign object debris (FOD). Through processing, handling, storage, and use, it is imperative to follow best practices to maintain cleanliness for final part properties. For spherical powder in AM technologies, additional steps and handling considerations are needed as particle shape and size distribution affect processing [7].
This paper reviews the three manufacturing regimes shown in Figure 3 with respect to oxygen control, powdersize and morphology, and cleanliness.For the purposes of this paper, the ‘powder processing’ and ‘handling and storage’ regimes will be covered in greatest detail, as these steps tie in most closely to achieving and maintaining the quality and purity of AM powders.
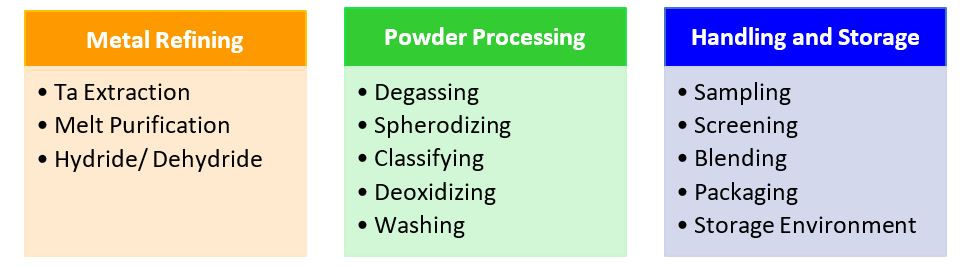
Metal Refining
The purification of tantalum beginswith refinement from ores including columbite, tantalite, pegmatite, and wodginite [8]. These ore materials contain a mixture of tantalum (Ta), niobium (Nb), lithium, iron, manganese, and beryllium with lower levels of other metallic and semi-metallic elements [9, 10]. While some elements such as niobium and tungsten may have little effect on key Ta properties, others can be detrimental to strength, corrosion resistance, and biologic inertness [11].
The production of pure tantalum is challenging due to low concentration sources and the processes needed to recover pure metal. Tantalum is not a commonly occurring element, making up only 1 to 2 ppm of the Earth’s crust and the number of Ta-bearing mines around the world is relatively small compared to other refractory elements [12, 13]. Tantalum ore is more challenging to process than other ores due to its elemental content and chemical resistivity. Due to the low levels of tantalum in ore bodies, tantalum ore is first concentrated by gravity separation. Subsequently, the tantalum concentrate is exposed to very acidic conditions using hydrofluoric acid to release Ta atoms. Solvent extraction and crystallization are performed to separate Ta from other elements and create a tantalum salt (K2TaF7) which is reduced to tantalum metal via reaction with sodium [19]. The reduced metal is cleaned to remove salts from the reduction process and then pressed into billets for electron beam (EB) melting. The metal is melted at over 4,000°C to remove most metallic impurities (except other refractories) as well as interstitial elements. The high-purity ingot is hydrided to make it brittle, crushed, and milled to size and degassed back to metal. Each of these steps requires careful considerations to prevent the introduction of FOD, cross-contamination from other products, and oxide/nitride formation. Attention to detail in the purification and powder preparation steps results in high quality feedstock for subsequent processing.
Powder Processing
Chemical and physical contamination must be controlled throughout all material processing stages, with morphology adding yet another critical factor into consideration. An effective method for contamination avoidance is physical separation of processing equipment and/or material(s). By removing the opportunity for cross-contamination, it is possible to maintain elemental and morphological purity. Table 1 lists many of the process steps required for the production of tantalum additive powders and the associated risk and mitigation factors.
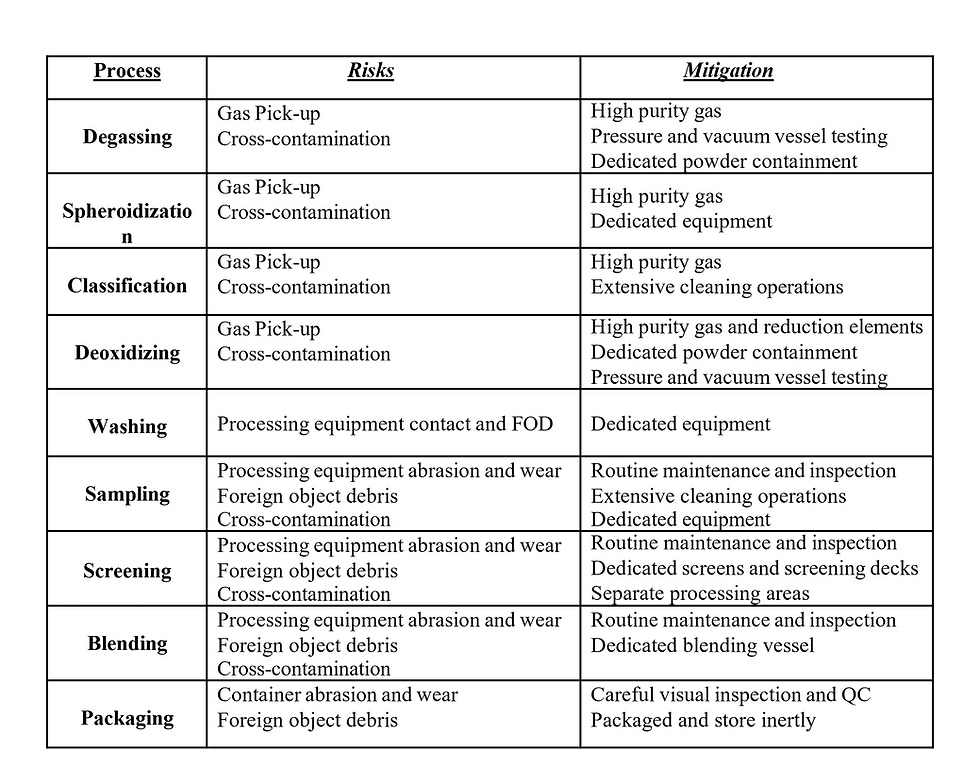
For many of the dynamic processes (screening, blending, and classification), the powders will come into contact with intricately designed stainless steel surfaces or non-metallic gaskets that have the potential to trap or hold powder and/or contaminates. For the screening of powders, stainless steel or nylon screens are used in multiple processing stages to remove fines and/or oversized particles, as well as any oversize FOD present within the material (Figure 4). The inherent design of many woven screens leads to particles potentially becoming trapped and cross contaminating future materials run on the same screen. Ideally it would be possible to simply clean and reuse these screens for all particle shapes and compositions, but the cross contamination risk to these high-value materials is too great, especially at later stages of processing. Saving cost by introducing multiple cleaning steps versus procuring product-specific equipment will open the door to contamination down the road if cleaning steps prove to be insufficient or unsustainable. A preferred approach is to retain product specific equipment and dedicated screens for each unique material within the metal AM powder manufacturing process.
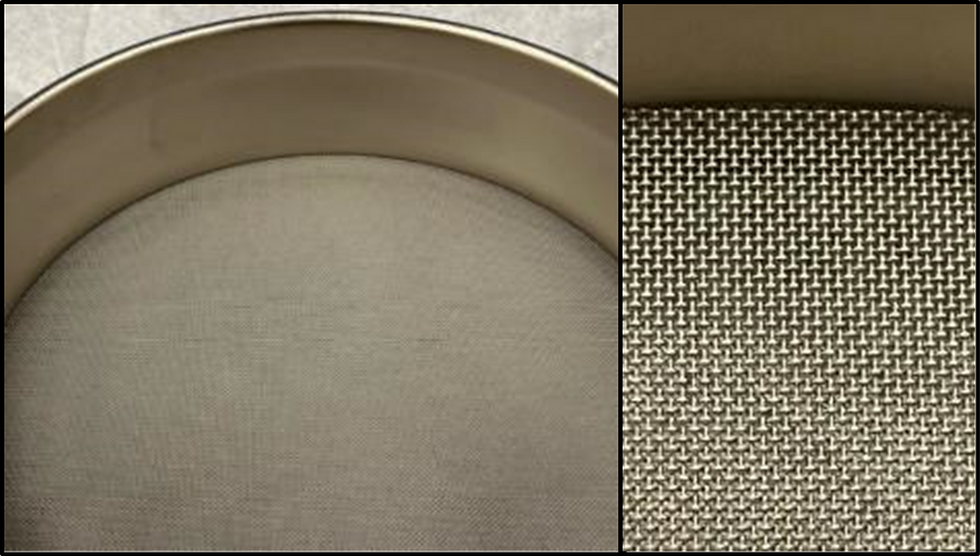
Spheroidization
Many technologies exist to spheroidize metallic powders; however,the unique challenge for Ta, Nb, and alloys thereof are the high melting temperatures and the propensity for oxide formation. Traditional methods of powder production such as gas atomization are not capable of producing low-oxygen, high- purity, fully dense powders. Research has shown that plasma spheroidized powders consistently achieve superior sphericity when compared to most other spheroidizing techniques [14, 15]. The sphericity, PSD, and open area fraction directly impact powder flowability, powder bed density, layer uniformity, and melting behavior, as well as the recoating time of the equipment for powder bed applications. All of these factors combined determine the overall homogeneity, density, build time, surface quality, print accuracy, resolution, printability limits, and mechanical properties of the printed components which are crucial for printing success [16]. For materials such as tantalum, carefully considering and monitor spheroidization, cleaning, and purification of the powder is critical to better ensure quality printed components and therefore build success rates.
Plasma spheroidized tantalum powders are typically produced in a continuous flow process converting a rough cut random shaped(angular) powder to uniform spherical geometry powder by a high temperature plasma. There are multiple vendors for plasma spheroidizing systems, with those from Tekna based on radio frequency (RF) plasma technology finding good acceptance. Feed powders are typically high purity angular powder which are initially screened to a desired PSD before the spheroidizing step. The RF plasma instantaneously superheats and melts the angular tantalum feed material leading to spheroidization due to surface tension forces As the spherical droplets fall away from the plasma torch, rapid solidification ensues locking in the spherical geometry. A small amount of material (metal and oxide) is vaporized within the plasma and condenses as nanoscale surface debris on the primary spherical particles. The particle size distribution of the spherical product closely follows the distribution of the angular feed material. Figure 5 shows a typical 15-45 µm, high-purity angular feed powder and the spherical powder that results after passing through a radio frequency plasma.

Post processing steps after spheroidization may be required to improve surface roughness and remove satellite particles. Figure 6 demonstrates that the powder directly from the plasma spheroidization is highly spherical and has a minimum amount of surface debris and satellite particles; however, utilizing proprietary cleaning steps will remove any small amount of nano-material from the surface.
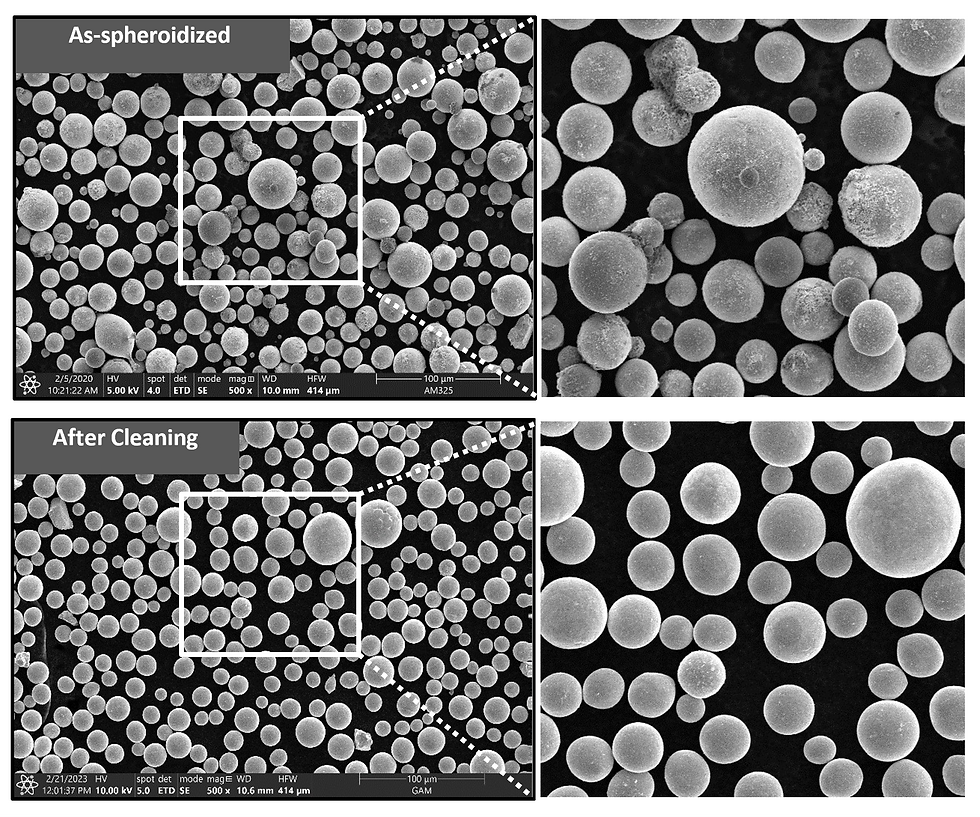
Deoxidation and Finishing
As previously discussed, tantalum powder oxygen content is very important for establishing initial mechanical properties and maintain those properties over the use of an AM tantalum powder. To create low oxygen powders, after spherodization the powder should undergo a deoxidation process. Deoxidation drives bulk oxygen out of the material and reacts it with a reducing element at temperatures between 600-1,000°C, depending on the particle morphology and size. After deoxidation and passivation, the powder is tumbled in acid and thoroughly washed to remove all reactant oxides and acid present. A key factor in the effectiveness of post deoxidation washing is the optimization of the ratio of reduction element to acid. Excess acid can increase the levels of nitrogen and hydrogen in the powder, but insufficient acid can result in incomplete removal of the reduction elements.
At the end of deoxidation and acid finishing, the powder should be at its highest level of purity and cleanliness. The oxygen content of the tantalum powder can be reduced to 150 ppm or lower ata PSD of 15-45 µm. Table 2 summarizes the high purity tantalum powders offered by GAM and their respective elemental levels and particle size distributions.
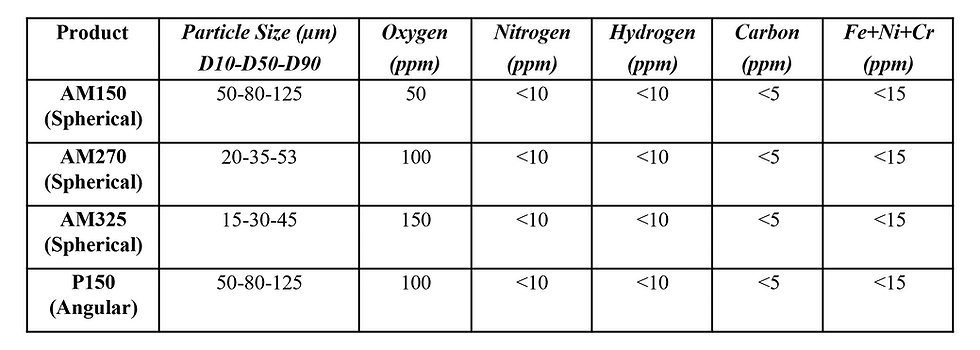
Even after the powders have been thoroughly purified and cleaned,there are many operations that still threaten the purity of the powders, such as blending, sampling, handling, and storage.
Handling and Storage
As discussed previously, the process to separate tantalum from other materials such as niobium is highly involved and requires the use of uncommon chemicals. To produce high purity tantalum powders, it is important to consider the processing and post-processing techniques. It is ever important to isolate materials and avoid irreversible contamination (such as are foreign non-magnetic metallic and/or angular particles within the targeted PSD and higher than targeted hydrogen, nitrogen, and carbon). The same considerations to process and produce tantalum powders come into play when storing the powders. The environment and packaging materials need to be carefully evaluated and considered to ensure materials arrive at the AM printer as pristine as when they were produced. Ongoing studies have shown that at room temperature, spherical tantalum powder does not readily oxidize and can be stored in a variety of containers without significant increase of oxygen contamination. (Figure 7) Surface area of powders do play a role, with higher surface area particles (smaller PSD and/or nonspherical shape) oxidizing more readily. Whatever size or shape of powder is being used,best practices should be employed to limit exposure to air and the possibility of contamination.
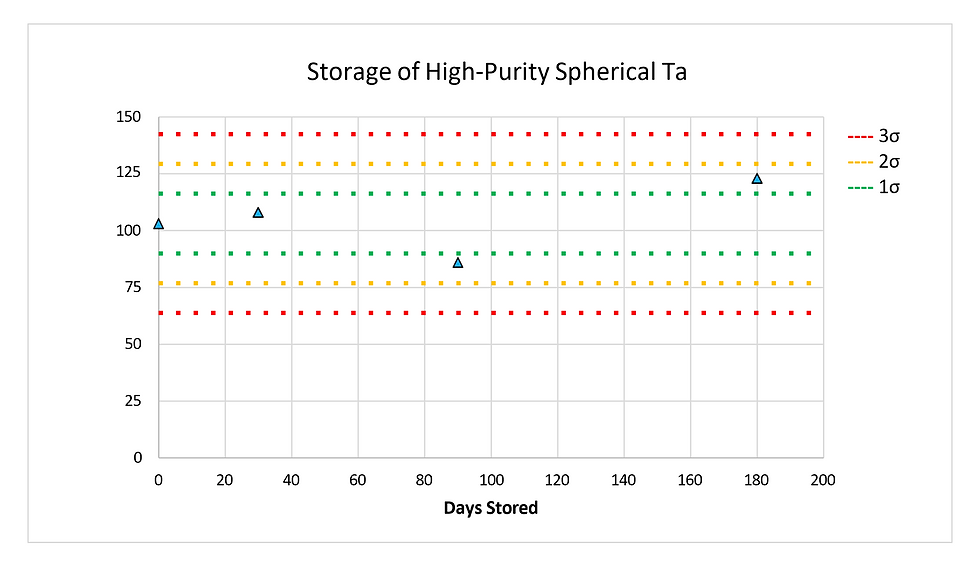
Summary
The very properties of tantalum and other refractory metals that make them highly sought after also make them difficult to purify and process. As the world continues to find new uses and applications through additive manufacturing, it becomes ever important for the upstream material producers to remain flexible. Creating highly spherical powders for additive requires a high purity spheroidization process, along with high-end cleaning, deoxidation, blending, and handling. This is often required for all powders used in AM but for high quality tantalum powders it is necessary to achieve the maximum number reuse cycles that can achieve >99% density and >99.5% material purity. Research and development has shown this to be possible [18] but it requires continued process development and testing as new techniques and new high cost refractory tantalum alloys are developed. Maintaining purity is challenging but not impossible. By identifying all of the potential risks to the powder and end product, processes and material can be designed to ensure longevity and cleanliness throughout its entire lifecycle.
REFERENCES (1) Sungail, Craig, and Aamir D. Abid. “Additive Manufacturing of Tantalum– a Study of Chemical and Physical Properties of Printed Tantalum.” Metal Powder Report, vol. 75, no. 1, 2020, pp. 28– 33., https://doi.org/10.1016/j.mprp.2019.03.001. (2) Sungail, Craig, and Aamir Abid.“Spherical Tantalum Feed Powder for Metal Additive Manufacturing.” Metal Powder Report, vol. 73, no. 6, 2018, pp. 316–318., https://doi.org/10.1016/j.mprp.2018.03.046. (3) Macagno, V., & Schultze, J. W. (1984). The growth and properties of thin oxide layers on tantalum electrodes. Journal of Electroanalytical Chemistry and Interfacial Electrochemistry, 180(1-2), 157–170. https://doi.org/10.1016/0368-1874(84)83577-7 (4) Tan, C., Shi, Q., Li, K., Khanlari,K., & Liu, X. (2023).Effect of oxygen content of tantalum powders on the characteristics of parts processed by laser powder bed fusion. International Journal of Refractory Metals and Hard Materials, 110, 106008. https://doi.org/10.1016/j.ijrmhm.2022.106008 (5) Shabalin, I.L. (2014).Tantalum. In: Ultra-High Temperature Materials I. Springer, Dordrecht. pp. 357–109., https://doi.org/10.1007/978-94-007-7587-9_6 (6) Guo, Y., Chen, C., Wang, Q., & Liu, M. (2021). Effects of reuse on the properties of tantalum powders and tantalum parts additively manufactured by electron beam powder bed fusion. Materials Research Express, 8(4), 046538.https://doi.org/10.1088/2053-1591/abf60e (7) Mussatto, A., Groarke, R., O’Neill, A., Obeidi, M. A., Delaure, Y., & Brabazon, D. (2021). Influences of powder morphology and spreading parameters on the powder bed topography uniformity in powder bed fusion metal additive manufacturing. Additive Manufacturing, 38, 101807. https://doi.org/10.1016/j.addma.2020.101807 (8) Papp, J. F. (2018, June 14). Mineral Resource of the Month: Tantalum.Retrieved April 24, 2023, from https://www.earthmagazine.org/article/mineral-resource-month-tantalum (9) Britannica, The Editors of Encyclopaedia. "tantalum". Encyclopedia Britannica, 18 Apr. 2023, https://www.britannica.com/science/tantalum. Accessed 24 April 2023. (10) Sun, Wenli, Zhidan Zhao, Xuanxue Mo, Chunjing Wei, Guochen Dong, Xiaowei Li, Wanming Yuan, Tao Wang, Shuang Yang, Bingzhang Wang, Tong Pan, Jie Han, Hongliang Cao, Yan Tang, and Liangliang Zhang. 2023. "Age and Composition of Columbite-Tantalite Group Minerals in the Spodumene Pegmatite from the Chakabeishan Deposit, Northern Tibetan Plateau and Their Implications" Minerals 13, no. 2: 201. https://doi.org/10.3390/min13020201 (11) TANTALUM-NIOBIUM INTERNATIONAL STUDY CENTER. (2013).Processing: Extraction and refining. Tantalum Processing | TIC. Retrieved from https://tanb.org/about- tantalum/processing-extraction-and-refining (12) Emsley, J. (2003). Nature's building blocks: An A-Z guide to the elements(Ser. Pg 420 - 421). Oxford University Press.
(13) Geoscience Australia. (2018, December 31). Tantalum. Geoscience Australia. Retrieved from https://www.ga.gov.au/scientific-topics/minerals/mineral-resources-and-advice/australian- resource-reviews/tantalum
(14) Wei, W.-H.,Wang, L.-Z., Chen, T., Duan, X.-M., & Li, W. (2017). Study on the flow properties of ti-6al-4v powders prepared by radio-frequency plasma spheroidization. Advanced Powder Technology, 28(9), 2431–2437. https://doi.org/10.1016/j.apt.2017.06.025
(15) Hossein Sehhat, M., Perez-Palomino, D., Wiedemeier, C., Cullom, T., Newkirk, J. W., & Leu,
M. C. (2023). Characterization of virgin, re-used,and oxygen-reduced copperpowders processed by the plasma spheroidization process. Advanced Powder Technology, 34(1), 103885. https://doi.org/10.1016/j.apt.2022.103885
(16) Brika, S. E., Letenneur, M., Dion, C. A., & Brailovski, V. (2020). Influence of particle morphology and size distribution on the powder flowability and laser powder bed fusion manufacturability of ti-6al-4v alloy. Additive Manufacturing, 31, 100929. https://doi.org/10.1016/j.addma.2019.100929
(17) Novotnak, D. J., & Lherbier,L. W. (n.d.). Euro PM2015 – AM – Properties and Failure Analysis
- The Impact of Recycling AM Powders. ms, Carpenter Powder Products.
(18) Sungail, C. M., & Abid, A. D. (2020, March 12). SPHERICAL TANTALUM POWDER ,
Publication Classification PRODUCTS CONTAINING THE SAME , AND METHODS OF MAKING THE SAME.
(19) “Processing: Extraction and Refining.” Tantalum Processing | TIC, tanb.org/about- tantalum/processing-extraction-and-refining.
Comments