Getting Started with Cold Spray
- ES3
- Apr 28, 2021
- 6 min read
Restoration of metallic parts with cold spray application began in the automotive industry. The Department of Defense (DoD) has taken notice of its ability to cheaply and swiftly repair and restore aircraft components. Engineering and Software System Solutions, Inc. (ES3), a woman-owned small business defense and aerospace support contractor headquartered in San Diego, CA, has been awarded multiple Small Business Innovation Research (SBIR) contracts to conduct in depth research to develop cold spray technologies and applications for providing dimensional and/or structural restoration. ES3 also evaluates in situ cold spray monitoring systems and assesses standard or novel non-destructive inspection (NDI) methods. This will allow Naval Stations and Air Force Bases to practice repairs using a standard produced from this study and feel confident in the technology with data produced from the research.
Under these SBIR efforts, ES3 is working with up to four different cold spray systems currently and other systems in the past. The current systems under development are both handheld and robotic and include Centerline’s SST Series P, XP, and EPX (low- and high-pressure systems), Inovati’s KM-CDS, and VRC’s Gen III. Each system is different from one another. Table 1 below provides characteristics of each system to show how they are different along with what powder ES3 is currently using for its contracts.
Table 1: Cold spray configurations for the four systems on the Navy Phase II.5& III follow on SBIR efforts.
Setting Up a Cold Spray Facility
Depending on the application setup can be as easy as shipping a system to you with simple install, or it can be as complex as designing a booth to the customer’s request and having a booth installed. Low-pressure systems typically are portable and are easily relocated for field level use. On the contrary, high-pressure systems typically require the use of a robot inside a booth for application. This would normally require a part that needs spraying to be shipped to the location; however, ES3 is tasked with translating high pressure robotic cold spray process parameters to a compatible handheld application. Figure 1 shows images of the three cold spray systems under development and evaluation.
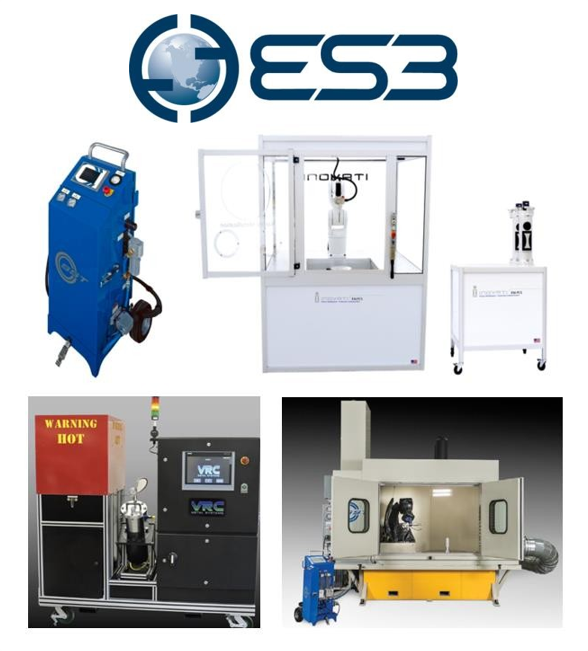
Figure 1. The four cold spray systems under evaluation in ES3’s Phase II.5 & III cold spray SBIR projects.
Safety Concerns
The biggest safety concern with cold spray is inhalation of the metallic powder while handling it. The powder particle size is very small, and the body cannot filter it before it reaches the lungs. Operators need to be aware of this and wear protective respiratory equipment. Other safety concerns would be generic robotic operating safety concerns when spraying with a robot. When spraying with a handheld system, operators need to be concerned with the high heat (up to 700 oC depending on powder) and loud noise that the systems generate while in use. These safety concerns are easily mitigated by wearing the appropriate personal protective equipment (PPE) and through proper training. ES3 has extensive experience in cold spray and can perform installation, develop operating parameters, and provide onsite training to ensure the safety of all equipment operators and maintainers.
Optimizing Parameters for Application
Before ES3 begins the cold spray process, ES3 will first conduct a parameter optimization study. The intent of this study is to spray test samples with changes to a single parameter at a time. After the samples are tested the parameter that provides the best results will be chosen as the set to use for the project. The primary operating parameters explored are temperature and pressure. Other parameters looked at are as follows: stand-off distance (how far the tip of the nozzle is from the applied surface), traverse speed (how fast the robot travels over the applied surface), step over or overlap (the distance the robot takes to spray the next row and powder overlap), and powder feed rate (how much powder is fed through the system). The parameters are major contributing factors to porosity and layer thickness after a single application. Initial particles have a stronger adhesion to the substrate and cohesion to other particles when subsequent particles push them deeper into the substrate or one another. Thus, the more layers applied the stronger the adhesion; however, there are limitations to adhesion strength.
Choosing the Correct Equipment
Material (Substrate & Powder)
Substrate and powder vary based upon customer request. Typically, ES3 uses the same substrate the customer plans to use the cold spray technology on. However, this does not mean every application will use the same type of powder material as the substrate. For example, ES3 is currently working on applying 6061 Solvus powder on H-60 gearbox replicas. This H-60 substrate material is magnesium, while the powder is 6061 aluminum alloy.
Powder is determined based on the application results needed (such as wear or corrosion resistance, replacement of hard chrome or anodize coatings, etc.), and the substrate the cold spray will be applied to. Currently, limited studies have been conducted to mix powders across systems. As mentioned earlier ES3 is spraying H-60 magnesium gear boxes. Sprays used on magnesium substrates require good corrosion resistance, as magnesium is highly anodic relative to nearly all other metals. Furthermore, weight is a consideration when spraying magnesium substrates which is why 6061 was used with the magnesium substrate.
Nozzles and Carrier Gas
Nozzle choice is dependent on the carrier gas. Systems will typically have two different sized orifice nozzles. A larger orifice nozzle is used when spraying with nitrogen (a larger particle), whereas a smaller orifice nozzle is used when spraying with helium. Data collected by ES3 shows that helium as a carrier gas creates a stronger bond with the powder and substrate. This is because the particle travels faster as helium has a higher speed of sound than nitrogen, and thus has a higher kinetic energy upon impact. Unfortunately, helium is around 10x the cost of nitrogen, so this trade-off must be considered when conducting research. ES3 completed a Phase I SBIR in the summer of 2020 to attempt to reduce this trade-off. Nozzles also come in different materials. Table 2 shows the different nozzle material ES3 uses with each system.
Table 2: Nozzle configurations for the different cold spray systems studied by ES3.
Tungsten nozzles are used for higher temperature sprays. Polymer nozzles can start deforming and have poor performance near 440 oC. Stainless steel nozzles are a cheaper route to take (about $30 a nozzle), as the tungsten and polymer nozzles can cost $2-3K. However, stainless steel nozzles break down at a much higher rate. Problems occurring with nozzles include clogs, deformation, and generic breaking. Clogs can form in a matter of minutes when spraying aluminum powder with a tungsten nozzle. They can also form on the cheaper stainless steel but take much longer to form. Clogs on a polymer nozzle are not created by powder buildup in the nozzle, but rather from the deformation of the nozzle. The polymer nozzle’s orifice will shrink as the material expands due to high temperature. To resolve this aluminum buildup in the nozzle, simply take the nozzles and place them in a sodium hydroxide solution for 24 hours. If the deformation issue is mild, simply take a drill bit and drill out the correct hole size; however, this can only be done a few times before the nozzle is beyond repair. Stainless steel nozzles can also form holes in them. Once this happens, they are unusable and must be tossed out. Figure 2 shows nozzles ES3 developed for the USAF for difficult to access applications.

Figure 2. Three different nozzles developed for difficult to access locations onboard USAF aircraft.
Cold Spray System
The two primary types of cold spray systems in industry are high- and low-pressure systems. The low- pressure systems spray anywhere between 90 and 250 psi, while the high-pressure systems can spray from 500 to 1000 psi. Coating performance characteristics, such as adhesion results, vary with each system and application, so selection of the system is a key factor during development. Systems are chosen based on the customers’ performance requirements, so ES3 develops coatings for their usage scenario so the data produced is relevant.
Other Studies (Gas Mixing)
ES3 is conducting a Phase II Navy SBIR effort where the goal is to find a way to reduce the cost of helium sprays without sacrificing performance results. ES3 has developed a prototype gas chamber mixture to combine both helium and nitrogen to spray at the same time. ES3 found that you can in fact have the two gases mixed and achieve similar results, thus saving significant cost. In this future study ES3 will utilize an automatic mixing chamber that will be used with low and high-pressure systems. ES3 will look further into the study with data such as what percent volume of nitrogen can be mixed with helium before the results deteriorate.
Monitoring and NDI
ES3 is also evaluating the commercial-of-the-shelf (COTS) cold spray monitoring systems to provide a ranked listing of NDI suppliers including pros, cons, observations, and recommendations. These in situ cold spray monitoring devices provide data that will help improve and more efficiently characterize cold spray particles using velocity, particle size, and particle density as data extracts for determining cold spray quality. This data provides ES3 with more information that will help determine the outcome of a spray without having to complete full metallurgical lab work. ES3 hopes they will be able to see correlation between particle velocity and particle density from a spray cycle. Lastly, ES3 is evaluating post processing cold spray NDI techniques. ES3 is conducting an industry review of existing techniques and develop a test plan for evaluating available post processing NDI techniques.
Kommentit